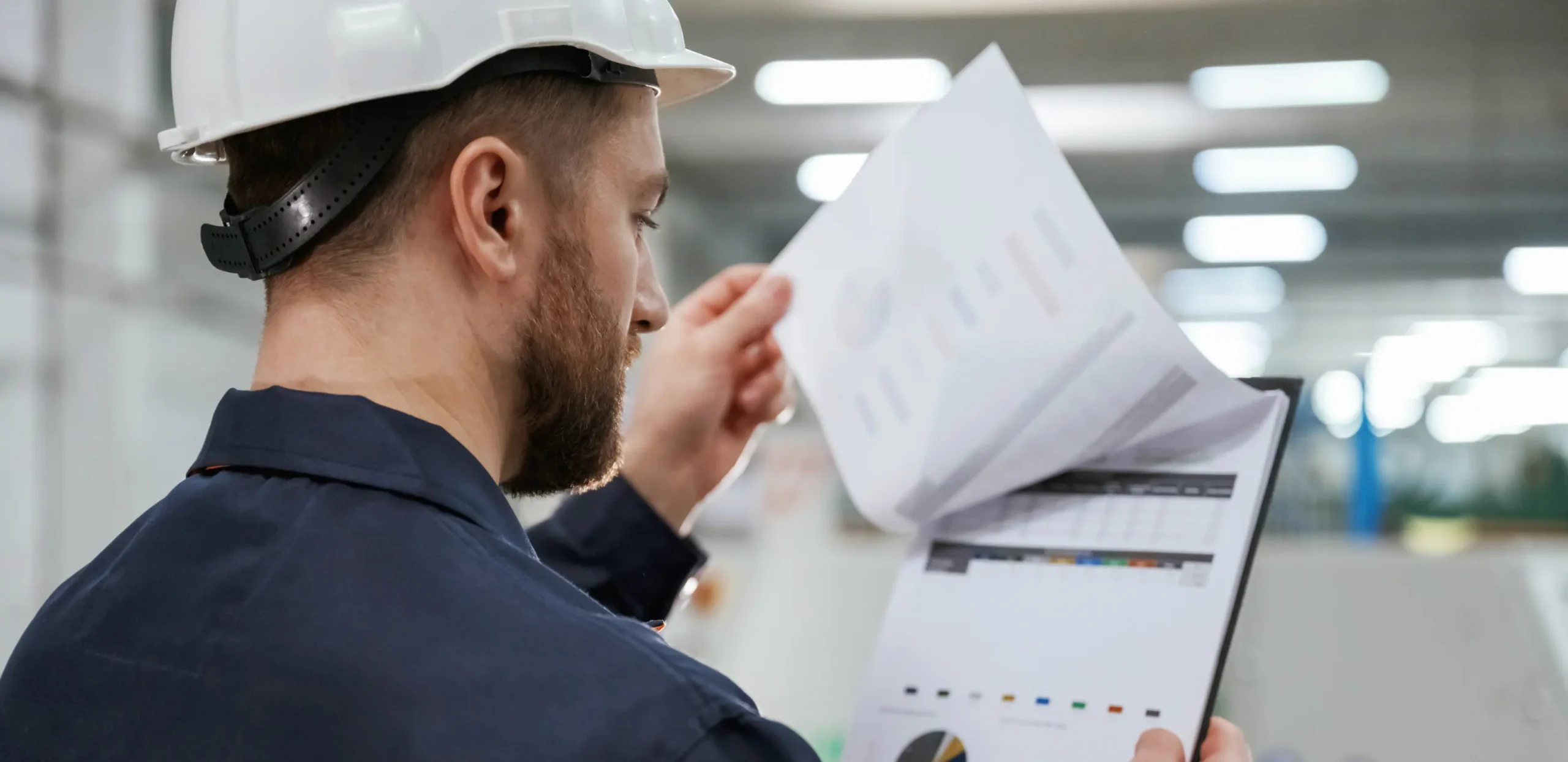
Step-by-step to master your supplier audit process
A robust and reliable supply chain serves as the backbone of any successful manufacturing operation. However, a smooth flow of parts and materials depends on one crucial, determining factor: effective supplier quality management.
Ensuring that suppliers consistently deliver products that meet the required specifications is essential for upholding quality control in your own finished goods and meeting industry standards. This is where a supplier audit checklist takes great importance.
Figure out the supplier audit checklist’s essentials with this article. Keep reading to learn more about your role as an SQE in the continuous improvement process.
Creating a supplier audit checklist, step-by-step
A supplier audit is a systematic evaluation of a supplier’s capabilities and practices to assess their commitment to quality. By conducting regular audits, manufacturers can identify potential performance risks, verify compliance with industry standards, and foster a collaborative relationship with suppliers to nurture the continuous improvement process.
Considering the various aspects it encompasses, creating a comprehensive supplier audit process can become a tricky task. Nonetheless, it’s a SQE’s greatest ally when done right.
To design the perfect supplier audit process for your quality assurance needs, begin by dividing the process into three main stages: pre-audit, on-site audit and post-audit.
Pre-audit preparation
Before diving into the audit itself, thorough preparation is key. Think of it as laying the groundwork for your evaluation and cementing the basis of success.
Here’s some pre-audit key aspects that your process should include:
- Supplier selection: Identify critical suppliers who significantly impact your manufacturing process. Prioritize audits for these high-risk vendors.
- Gather information: Collect supplier documentation like quality manuals, active certifications (ISO 9001:2015, Lean Six Sigma), and past performance data.
- Develop audit objectives: Define the goals you aim to achieve for each supplier audit. Common objectives include verifying quality control procedures, evaluating potential risk areas, and identifying opportunities for continuous improvement.
- Prepare audit team: Assemble a qualified team with expertise in quality management, current industry standards, and the ability to interpret the audit’s findings.
On-site audit
When you’re done gathering information and preparing for the audit, it’s time to conduct an on-site evaluation and delve further into the supplier’s quality management system. This is the crucial part of your supplier audit process. Here are key areas to assess:
- Quality Management System (QMS): Review the supplier’s documented QMS procedures and confirm their alignment with industry standards. Assess the effectiveness of their quality control and continuous improvement processes.
- Document and record control: Verify the proper creation, maintenance, and management of documents related to quality control procedures, inspections, and corrective actions. Ensure traceability of records throughout the manufacturing process.
- Control of Non-Conforming Materials (NCM): Evaluate the supplier’s procedures for identifying, segregating, and handling non-conforming materials. Verify their effectiveness in preventing NCMs from reaching your production line.
- Corrective Action and Preventive Action (CAPA): Assess the supplier’s process for identifying and addressing quality assurance issues. Check if they have a system for implementing corrective actions and preventing potential problems.
- Calibration and maintenance: Verify that measuring and test equipment used for quality control are calibrated and maintained according to industry standards.
- Supplier training protocols: Evaluate the training provided to personnel involved in quality control activities. Ensure they have the necessary skills and knowledge to perform their duties effectively. Inquire about continuing education programs.
Continuous improvement: Assess the supplier’s commitment to continuous improvement according to their quality management system. Search for recorded evidence of ongoing process improvement initiatives.
Post-audit activities
However, a supplier audit doesn’t end with an on-site visit. Once you’ve conducted the evaluation and gathered the necessary information you’ll have to interpret findings and consider further actions. Here are crucial post-audit steps to consider:
- Compile audit report: Properly document all audit findings, observations, and potential non-conformities in a comprehensive report.
- Corrective action plan: Work with the supplier to develop a corrective action plan for any identified non-conformities. Establish clear timelines and responsibilities for implementing corrective actions and continuous improvement processes.
- Follow-up audit: Monitor the supplier’s progress in implementing and maintaining the corrective action plan. Verify its effectiveness in addressing the root cause of noted non-conformities, according to the audit report.
Additional considerations
Supplier audits range from the automotive, to the electronic, to the aeronautic manufacturing business. So, beyond core QMS elements, some additional considerations might be relevant depending on your industry’s specific needs. For example:
- Supply chain management: Evaluate the supplier’s own supplier selection process and quality assurance practices for their raw materials.
- Inventory management: Assess the supplier’s inventory quality control procedures to ensure proper material handling and storage to prevent damage or deterioration.
- Environmental management: Evaluate the supplier’s commitment to environmental sustainability practices throughout their manufacturing process. Ensure their operations comply with current environmental laws and industry guidelines.
- Social responsibility: Assess the supplier’s adherence to ethical labor practices and responsible conflict mineral sourcing, if relevant to your company’s values.
By implementing a comprehensive supplier audit process, manufacturers can gain valuable insights into their supplier’s performance capabilities, commitment to quality and compliance with industry standards. This proactive approach strengthens supply chain resilience, minimizes risks, and fosters long-term partnerships with reliable suppliers.
Understanding supplier quality assurance as an ongoing process keeps companies competitive and innovative. Maintaining good practices is the key to being at the forefront of the industry, and having the finest quality management tools is the best way to do that.
Regular supplier audits, and clear communication and collaboration, coupled with a cloud-based full quality management solution like Kiuey, pave the way for continuous improvement and consistent quality across your manufacturing operations.
Manage all your supplier quality processes in the same place, on-demand, and flexible. Schedule a demo and start saving time and money with Kiuey.
Subscribe to our newsletter.
Your go-to destination for insights, best practices, and innovative solutions in supplier quality assurance.
Recent Posts
How Kiuey simplifies PPAP and APQP compliance
August 21, 2025
AIAG vs VDA AIAG PFMEA? Know the differences between
July 23, 2025
Categories
Let's talk to see how PPAP Manager can help your company to save time and money.