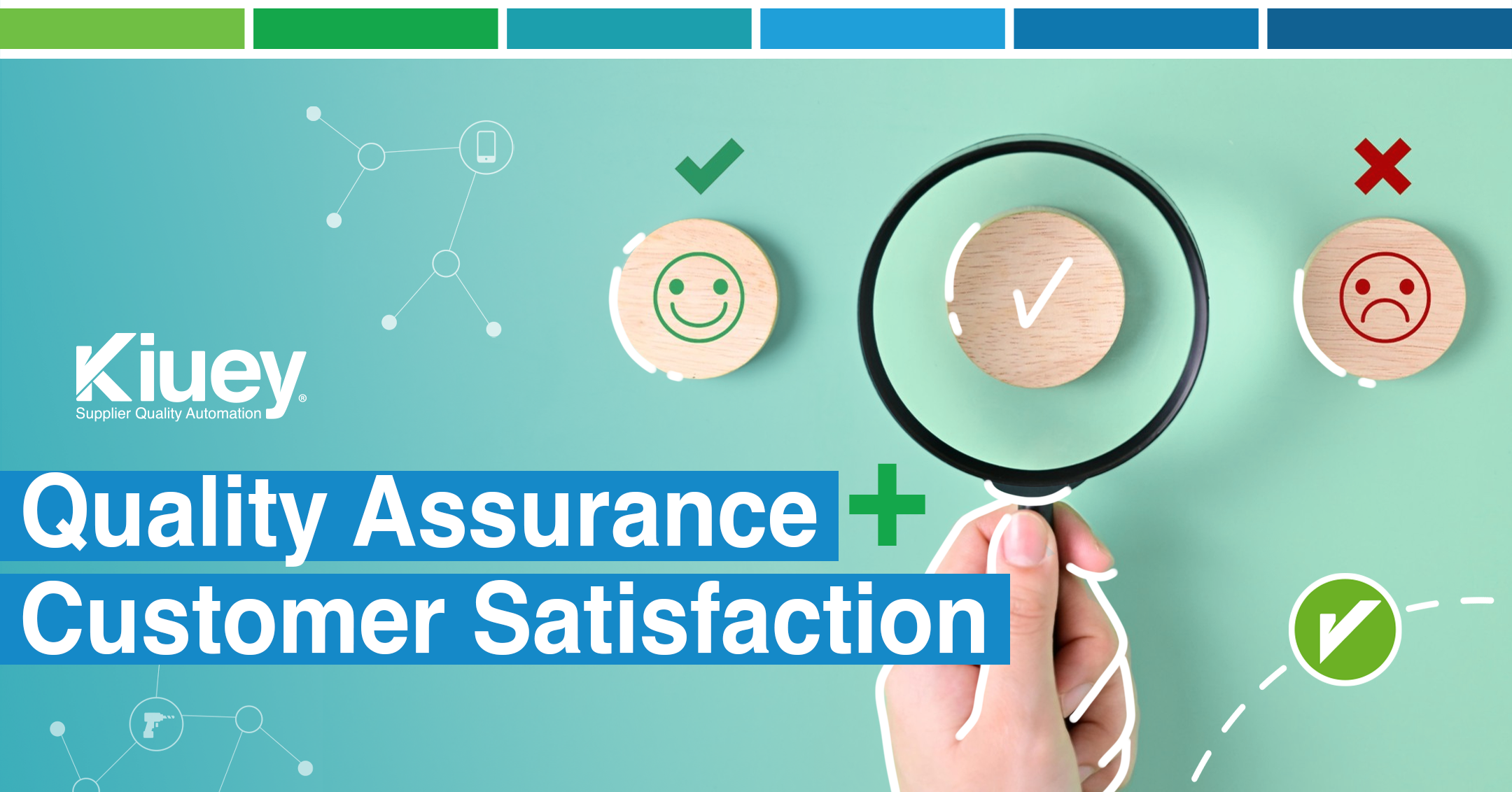
In today’s fiercely competitive market, customer satisfaction has become the cornerstone of business success. For manufacturers, delivering products that not only meet but exceed customer expectations is paramount. This is where quality assurance (QA) plays a pivotal role. By ensuring that products are consistently reliable, durable, and meet specified requirements, QA directly impacts customer satisfaction and loyalty.
Understanding the Customer Perspective
The first step to linking QA to customer satisfaction is to deeply understand customer needs and expectations. This involves market research, customer feedback analysis, and competitive benchmarking. By gaining insights into what customers value, manufacturers can align their QA processes accordingly.
For instance, if customer surveys reveal that product durability is a top concern, QA teams can focus on implementing rigorous testing procedures to assess product lifespan and resistance to wear and tear. Similarly, if customers prioritize aesthetics, QA can incorporate visual inspections and customer feedback mechanisms to ensure products meet desired appearance standards.
Building a Quality-Centric Culture
Creating a quality-centric culture throughout the organization is essential for achieving high levels of customer satisfaction. This involves fostering a shared commitment to quality at all levels, from management to the shop floor. Employees should be empowered to identify and address quality issues, and their contributions should be recognized and rewarded.
Implementing continuous improvement initiatives, such as Lean Six Sigma, can help to create a culture of quality. These methodologies focus on eliminating defects, reducing waste, and improving efficiency, all of which contribute to enhanced customer satisfaction.
Leveraging Technology
Technology can be a powerful tool for linking QA to customer satisfaction. Advanced quality management systems (QMS) can help to track product performance, identify trends, and implement corrective actions. Additionally, data analytics can be used to analyze customer feedback and correlate it with product quality metrics.
For example, manufacturers can use predictive analytics to identify potential quality issues before they impact customers. By analyzing production data, QA teams can predict when equipment is likely to fail or when product defects might occur. This proactive approach allows for timely intervention and prevents customer dissatisfaction.
Closing the Feedback Loop
Effective QA involves a closed-loop process that begins with customer feedback and ends with product improvement. By actively seeking and analyzing customer input, manufacturers can identify areas for improvement and make necessary adjustments to their QA processes.
Customer relationship management (CRM) systems can be used to collect and manage customer feedback. This information can then be shared with QA teams to inform product development and quality improvement initiatives. Additionally, social media monitoring can provide valuable insights into customer sentiment and identify potential quality issues.
Measuring and Monitoring Customer Satisfaction
To assess the effectiveness of QA efforts in driving customer satisfaction, manufacturers must establish key performance indicators (KPIs) and regularly monitor customer satisfaction metrics. These metrics can include customer satisfaction scores, net promoter scores, and customer retention rates.
By tracking these metrics over time, manufacturers can measure the impact of QA initiatives on customer satisfaction and identify areas for improvement. This data-driven approach ensures that QA efforts are aligned with business goals and customer expectations.
In conclusion, linking quality assurance to customer satisfaction is a critical component of manufacturing success. By understanding customer needs, fostering a quality-centric culture, leveraging technology, closing the feedback loop, and measuring performance, manufacturers can create products that delight customers and build long-term loyalty.
Subscribe to our newsletter.
Your go-to destination for insights, best practices, and innovative solutions in supplier quality assurance.
Recent Posts
AIAG vs VDA AIAG PFMEA? Know the differences between
July 23, 2025
The role of SCAR/CAPA in supplier risk management
July 10, 2025
Categories
Let's talk to see how PPAP Manager can help your company to save time and money.