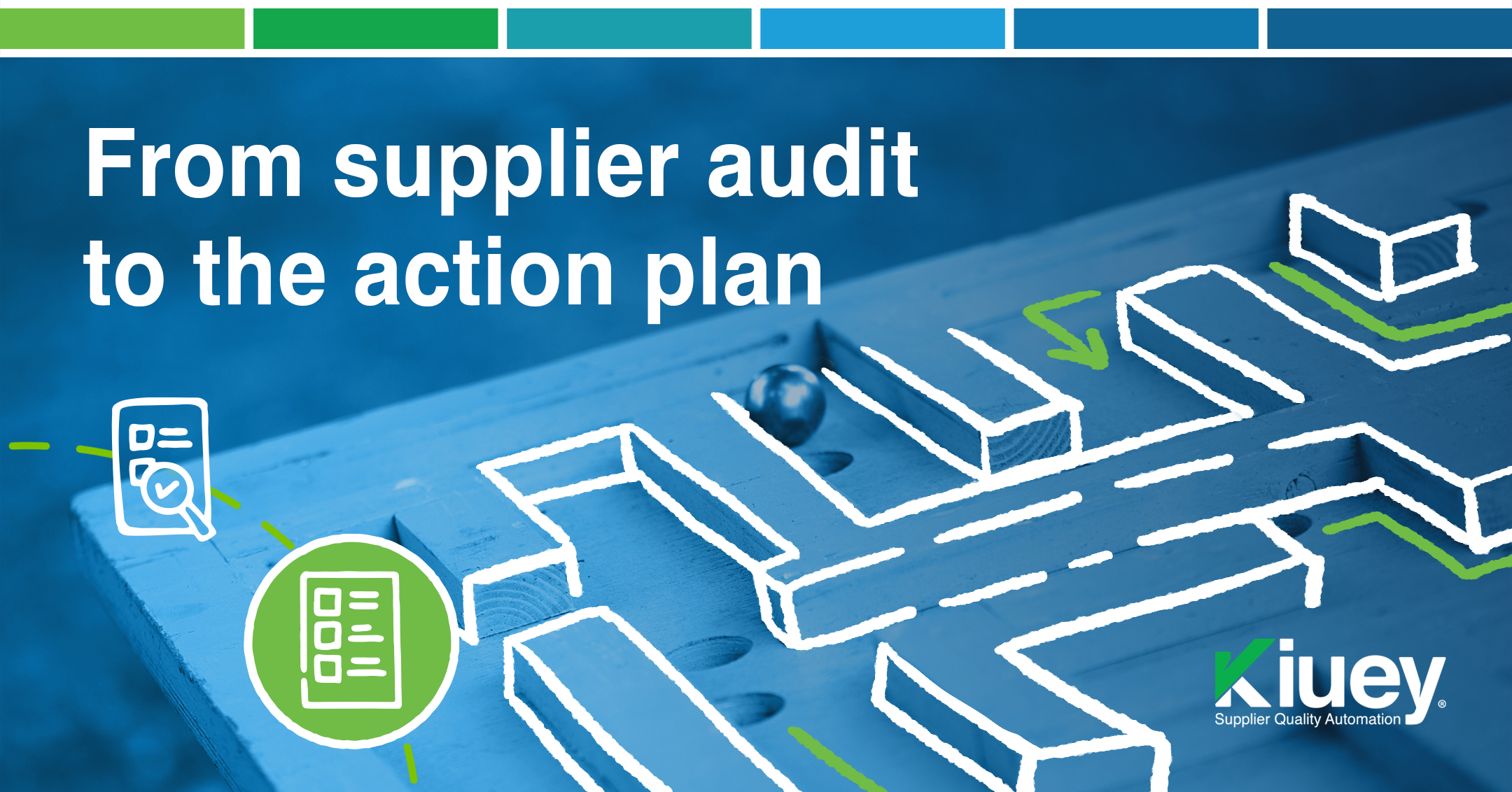
Supplier quality audits are essential for ensuring the smooth functioning of your supply chain. By evaluating a supplier’s adherence to quality standards, you can identify potential risks and ensure your products meet customer expectations. A crucial element of any successful audit is a well-defined action plan. This plan outlines the steps needed to address any non-conformances identified during the audit and lays the groundwork for continuous improvement.
Before the execution of the supplier audit, SQEs widely know that everything resides on 3 steps:
- Performing the pre-audit data collection and risk assessment
- Defining audit objectives and scope
- Selecting the audit team and assigning roles
How to develop an action plan after supplier audit?
Here’s a breakdown of the key processes involved in developing a robust action plan after supplier audit:
1. Identifying Non-Conformances based on the audit
During the audit, the team will evaluate the supplier’s QMS against pre-determined criteria. This may involve document reviews, facility tours, observation of production processes, and interviews with key personnel. Any deviations from agreed-upon standards or industry regulations are documented as non-conformances.
2. Developing Corrective Action Requests (CARs)
For each non-conformance identified, a corrective action request (CAR) should be created. A CAR details the specific issue, the potential impact on quality, and the required corrective action. It should also include a timeline for implementation and a designated person responsible for overseeing the corrective action process.
3. Negotiating and Finalizing the Action Plan
The audit team and the supplier will work together to finalize the action plan. This involves discussing the proposed corrective actions, timelines, and any necessary resources to ensure their effectiveness. Open communication and a collaborative approach are key to achieving a mutually agreeable plan.
4. Documentation and Follow-Up
A comprehensive report documenting the audit findings, including all identified non-conformances and the agreed-upon corrective actions, should be prepared. This report serves as a reference point for monitoring the supplier’s progress in implementing the action plan.
5. Monitoring and Verification of Corrective Actions
Following the audit, it’s crucial to monitor the supplier’s progress in implementing the corrective actions outlined in the plan. This may involve follow-up audits, reviewing documentation of completed actions, and evaluating the effectiveness of the implemented changes.
Effective Communication is Key for the action plan after supplier audit
Maintaining clear and consistent communication throughout the entire process is essential. Before the audit, ensure the supplier understands the objectives and scope. During the audit, promptly communicate any identified non-conformances and provide clear expectations for corrective actions. After the audit, maintain open communication channels to facilitate progress updates and address any challenges the supplier may encounter while implementing the action plan.
Building a Long-Term Partnership
Supplier quality audits are not punitive exercises. They serve as a valuable tool for identifying opportunities for improvement and fostering a collaborative partnership with your suppliers. A well-defined action plan demonstrates your commitment to working together to address quality issues and build a more robust supply chain.
By following these processes and fostering open communication, you can develop a strong action plan that addresses non-conformances identified during a supplier quality audit. This will ultimately lead to a more reliable and efficient supply chain, ensuring consistent quality for your products and services.
Subscribe to our newsletter.
Your go-to destination for insights, best practices, and innovative solutions in supplier quality assurance.
Recent Posts
PPAP management and how can Kiuey aid you
June 19, 2025
How to create a CAPA report that gets results
June 18, 2025
Categories
Let's talk to see how PPAP Manager can help your company to save time and money.