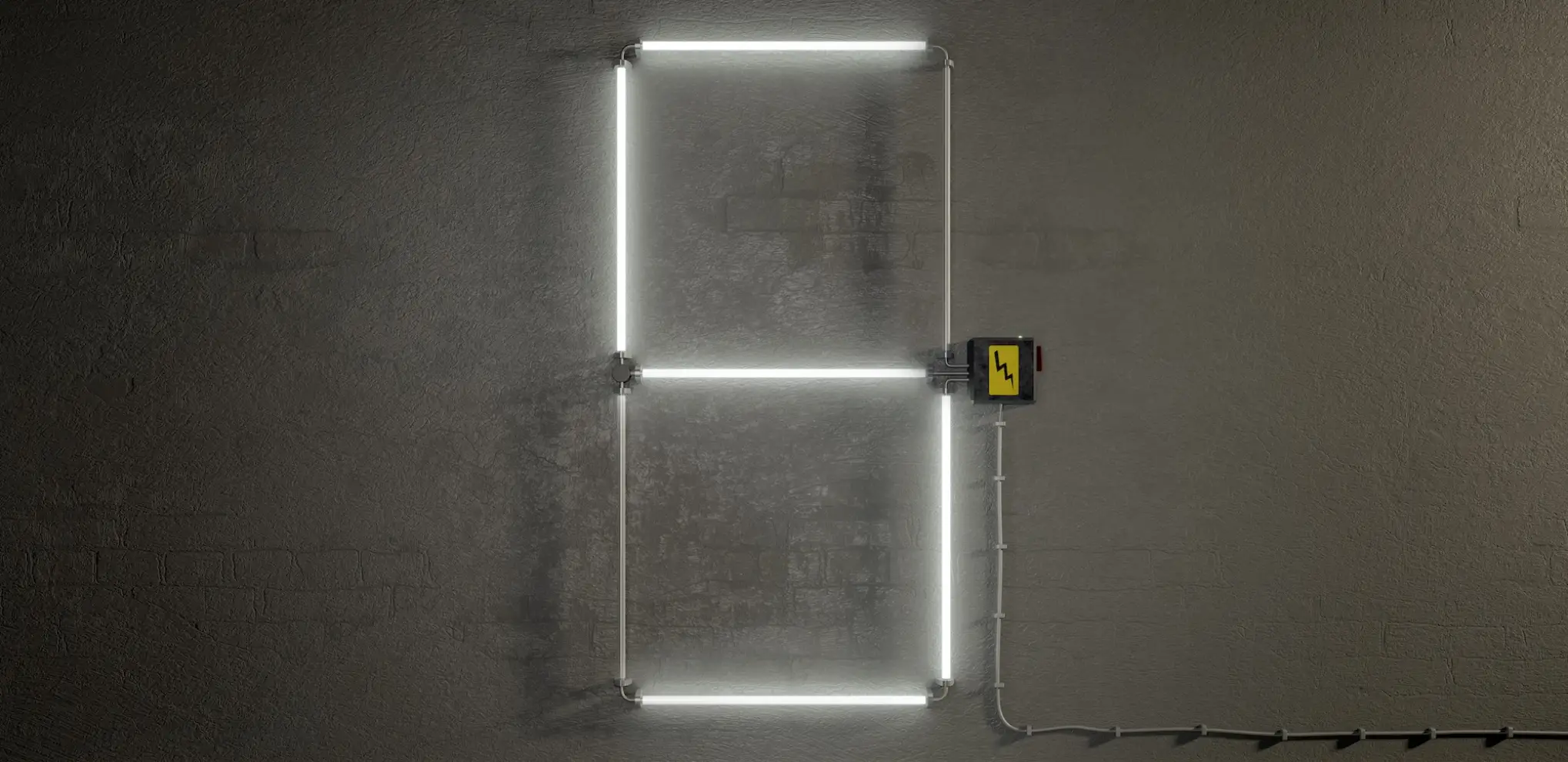
A guide to conquering PPAP Level 5 submission
The Production Part Approval Process (PPAP) is the cornerstone of quality control in the automotive and aerospace industries. Level 5, the most demanding, ensures complete documentation and on-site verifiability for critical parts in the supply chain.
Contrary to level 3, which calls for a Part Submission Warrant (PSW) with product samples and all supporting documentation, PPAP Level 5 involves a more rigorous process. It requires an additional on-site review at the suppliers’ manufacturing facility, meaning the customer can directly inspect the production process and verify the quality of the parts being made.
If you’re a supplier looking for ways to accomplish a smooth PPAP Level 5 submission, keep reading. In this article we cover what PPAP documents, requirements, and tips you’ll need on how to prepare accordingly to navigate the highest PPAP levels of scrutiny.
Understanding PPAP Level 5 submission requirements
PPAP Level 5 submission involves a comprehensive PPAP document package, containing all 18 elements outlined in the manual published by the AIAG (Automotive Industry Action Group) —the utmost resource for PPAP information within the automotive industry.
- Design records: These documents provide a detailed history of the part’s design, including engineering drawings, material specifications, and any design changes.
- Engineering change documents, if applicable:
- Customer engineering approval, if applicable: This document confirms the customer’s acceptance of any deviations from the original design specifications.
- Design Failure Mode and Effects Analysis (DFMEA):
- Process flow diagram: This chart visually depicts the entire production process, highlighting key steps, control points, and potential failure modes.
- Process Failure Mode and Effects Analysis (PFMEA): This analysis identifies potential failure modes in the production process, detailing their severity, occurrence, and detectability, and outlines plausible mitigation strategies.
- Control plan: Stems from the PFMEA. This plan details all inspection methods required to deliver products that continually meet the customer quality requirements.
- Measurement System Analysis (MSA): These reports demonstrate the accuracy and repeatability of the measuring equipment used for quality control.
- Dimensional results: This section provides documented measurements of the produced parts, verifying adherence to the specified tolerances.
- Material test reports: These reports showcase the results of tests conducted on the materials used in the part, confirming they meet the required properties.
- Initial process studies: These studies demonstrate that the critical processes are stable, demonstrate normal variation and are running near the intended nominal value.
- Qualified laboratory documentation: Documents and industry certifications verifying the material properties and composition used in the part’s production.
- Appearance Approval Report (AAR), if applicable: This report documents the customer’s approval of the part’s visual characteristics, such as color, finish, and texture.
- Sample product: These are sent for approval and are typically stored at either the customer or supplier’s site after the product development is complete.
- Master sample: The final sample of the product that is inspected and signed off by the customer. It serves as a benchmark for quality control throughout production.
- Checking aids: A comprehensive list of all the tools used to inspect, test or measure parts during the assembly process, including calibration schedules.
- Customer specific requirements: This list element is destined to any additional documents or data specifically requested by the customer.
- Part Submission Warrant (PSW): This document acts as the official cover sheet, summarizing the submitted PPAP documents and requesting customer approval.
Building a winning strategy
A successful PPAP Level 5 submission hinges on thorough preparation, implementing the right tools, and effective collaboration between supplier and customer. We recommend you consider some of the following aspects before embarking on this journey.
Get an early start
- Gather requirements: Obtain a clear understanding of the customer’s expectations. Review the purchase order, drawings, and any additional quality specifications.
- Form a cross-functional team: Assemble a team comprising representatives from engineering, quality control, production, and documentation departments. This ensures clear communication and a holistic approach.
- Documentation review: Thoroughly review all existing documentation related to the part and the production process. Ensure completeness and accuracy.
- Gap analysis: Identify any missing documents or areas where additional data is required to fulfill all PPAP Level 5 requirements.
- Develop missing documents: Focus on creating any missing documents, such as control plans, measurement system analysis reports, and process flow diagrams.
- Data collection and analysis: Gather and document the necessary data points, including dimensional results, material test reports, and initial sample inspection results.
- Customer communication: Maintain consistent communication with the customer throughout the process. Address any questions or concerns promptly.
Streamline the process
- Use templates: Leverage readily available PPAP templates to expedite document creation. Many industry organizations provide standardized templates.
- Electronic documentation: Take advantage of electronic document management systems to store and access PPAP documents efficiently.
- Training and awareness: Provide training to relevant personnel on PPAP Level 5 requirements and proper documentation procedures.
- Internal audits: Conduct regular internal audits to proactively identify and address any potential gaps in documentation or quality control procedures.
- Continuous improvement: Embrace a culture of continuous improvement within your organization. Regularly review and update PPAP procedures to reflect best practices and changing customer requirements.
Harness the power of collaboration
- Open communication: Maintain open communication channels with the customer throughout the process. Provide timely updates and address any concerns promptly.
- Customer involvement: Encourage customer participation during the development and review of PPAP documents. This ensures alignment with their expectations.
- Joint problem-solving: Approach any challenges or discrepancies with a collaborative problem-solving mindset. Focus on finding mutually agreeable solutions.
A meticulous PPAP Level 5 submission demonstrates your commitment to quality and process excellence, but building a robust strategy takes time and effort. Follow these tips to lay a strong foundation for a successful submission, and long-term partnership with your customers.
Discover how Kiuey’s PPAP Manager software solution can make your life easier as a quality engineer constantly managing PPAP documents and approvals. Gather all relevant information in one place, work collaboratively and optimize processes, while saving time and money.
Schedule a free demo today and try a new, better way to handle all your quality management needs. Transform the manufacturing industry one process at a time, with Kiuey.
Subscribe to our newsletter.
Your go-to destination for insights, best practices, and innovative solutions in supplier quality assurance.
Categories
Let's talk to see how PPAP Manager can help your company to save time and money.