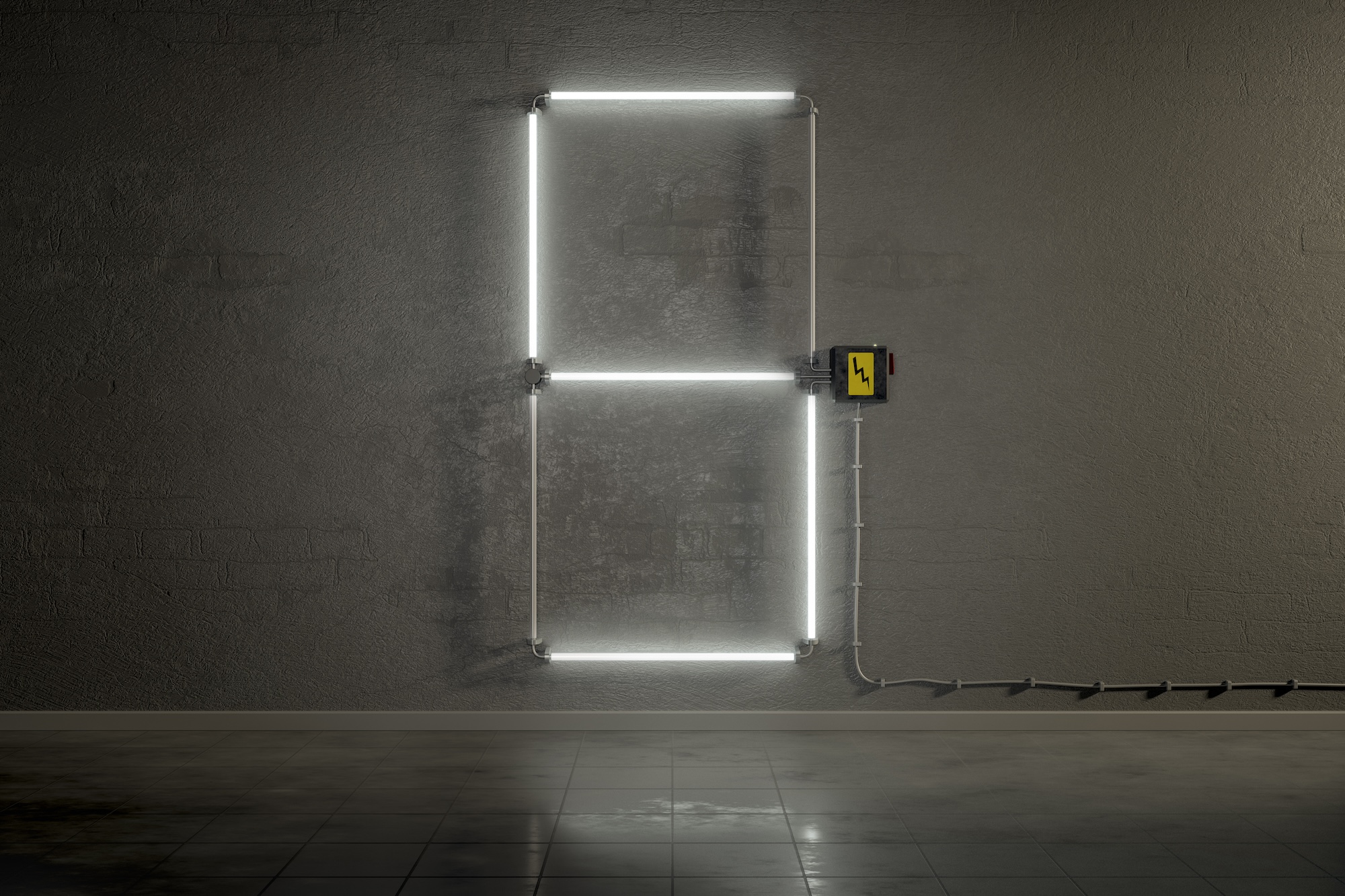
The Production Part Approval Process (PPAP) is the cornerstone of quality control in the automotive and aerospace industries. Level 5, the most demanding level, ensures complete documentation and on-site verifiability for critical parts. This article equips you, the supplier, for a smooth PPAP Level 5 submission, guaranteeing customer confidence and a successful project launch.
Understanding PPAP Level 5 Submission requirements
First of all, it’s important to understand the differences between PPAP levels. For example, PPAP Level 3 requires submitting a Part Submission Warrant (PSW) with product samples and all supporting documentation, while a PPAP Level 5 requires the same documentation, but with an additional on-site review at the supplier’s manufacturing facility, meaning the customer can directly inspect the production process and verify the quality of the parts being made; essentially, Level 5 is a more rigorous process with a higher level of scrutiny compared to Level 3.
PPAP Level 5 Submission signifies a comprehensive PPAP package containing all 18 elements outlined by the AIAG (Automotive Industry Action Group). While the specific documents requested may vary based on customer specifications, a solid understanding of the core elements is essential:
- Part Submission Warrant (PSW): This document acts as the official cover sheet, summarizing the submitted documents and requesting customer approval.
- Design Records: These documents provide a detailed history of the part’s design, including engineering drawings, material specifications, and any design changes.
- Process Flow Diagrams: These charts visually depict the entire production process, highlighting key steps, control points, and potential failure modes.
- Control Plans: These plans detail the inspection methods and procedures used to ensure parts meet all dimensional and quality specifications.
- Measurement System Analysis Reports (MSA): These reports demonstrate the accuracy and repeatability of the measuring equipment used for quality control.
- Dimensional Results: This section provides documented measurements of the produced parts, verifying adherence to the specified tolerances.
- Material Test Reports: These reports showcase the results of tests conducted on the materials used in the part, confirming they meet the required properties.
- Initial Sample Inspection Report (ISIR): This report details the results of the initial inspection of the produced parts, comparing them against the specifications.
- Appearance Sample Approval Report (if applicable): This report documents the customer’s approval of the part’s visual characteristics, such as color, finish, and texture.
- Customer Engineering Approval (if applicable): This document confirms the customer’s acceptance of any deviations from the original design specifications.
- Record of Waiver (if applicable): This document details any specific requirements waived by the customer and the justification for such waivers.
- Simulation Studies (if applicable): This section includes any simulations or analyses conducted to predict the part’s performance under various conditions.
- Manufacturing Location Layout: This provides a physical layout of the manufacturing facility where the parts are produced.
- Material Certification: Documents verifying the material properties and composition used in the part’s production.
- Customer Specific Requirements: Any additional documents or data specifically requested by the customer.
- Process FMEA (Failure Mode and Effects Analysis): This analysis identifies potential failure modes in the production process and outlines mitigation strategies.
- PFMEA Results: This section details the results of the process FMEA, including the severity, occurrence, and detectability of potential failures.
- Corrective Action Report (if applicable): This report documents any corrective actions taken to address identified issues during the production process.
Building a Winning Strategy
Early preparation is key to a successful PPAP Level 5 submission. Here are crucial steps to follow:
- Gather Requirements: Obtain a clear understanding of the customer’s expectations. Review the purchase order, drawings, and any additional quality specifications provided.
- Cross-Functional Team Formation: Assemble a team comprising representatives from engineering, quality control, production, and documentation departments. This ensures clear communication and a holistic approach.
- Documentation Review: Thoroughly review all existing documentation related to the part and the production process. Ensure completeness and accuracy.
- Gap Analysis: Identify any missing documents or areas where additional data is required to fulfill all Level 5 requirements.
- Develop Missing Documents: Focus on creating any missing documents, such as control plans, measurement system analysis reports, and process flow diagrams.
- Data Collection & Analysis: Gather and document the necessary data points, including dimensional results, material test reports, and initial sample inspection results.
- Customer Communication: Maintain consistent communication with the customer throughout the process. Address any questions or concerns promptly.
Streamlining the Process
Several practices can enhance efficiency and streamline the PPAP Level 5 submission process:
- Utilize Templates: Leverage readily available PPAP templates to expedite document creation. Many industry organizations provide standardized templates.
- Electronic Documentation: Utilize electronic document management systems to store and access PPAP documents efficiently, just as PPAP Manager by Kiuey.
- Training & Awareness: Provide training to relevant personnel on PPAP requirements and proper documentation procedures.
- Internal Audits: Conduct regular internal audits to proactively identify and address any potential gaps in documentation or quality control procedures.
- Continuous Improvement: Embrace a culture of continuous improvement within your organization. Regularly review and update PPAP procedures to reflect best practices and changing customer requirements.
The Power of Collaboration
A successful PPAP Level 5 submission hinges on effective collaboration between the supplier and the customer. Here are some key points to remember:
- Open Communication: Maintain open communication channels with the customer throughout the process. Provide timely updates and address any concerns promptly.
- Customer Involvement: Encourage customer participation during the development and review of PPAP documents. This ensures alignment with their expectations.
- Joint Problem-Solving: Approach any challenges or discrepancies with a collaborative problem-solving mindset. Focus on finding mutually agreeable solutions.
Conclusion
A meticulous PPAP Level 5 submission demonstrates your commitment to quality and process excellence. By following the outlined steps, building a robust preparation strategy, and fostering strong customer relationships, you can ensure a smooth submission process and lay the foundation for a successful long-term partnership with your customer. Remember, a well-documented and verified Level 5 PPAP submission instills confidence in your capabilities, paving the way for a successful project launch and a thriving business relationship.
Subscribe to our newsletter.
Your go-to destination for insights, best practices, and innovative solutions in supplier quality assurance.Recent Posts
AI + Calibration: Towards a standard digital calibration certificate
October 21, 2024
Project Management Basics for Supplier Quality Engineers
October 19, 2024
IMDS: A strategic tool for supplier quality engineers
October 16, 2024
ABC on ISO/IEC 17025 Calibration Certificates
October 14, 2024
Tags
Let's talk to see how PPAP Manager can help your company to save time and money.