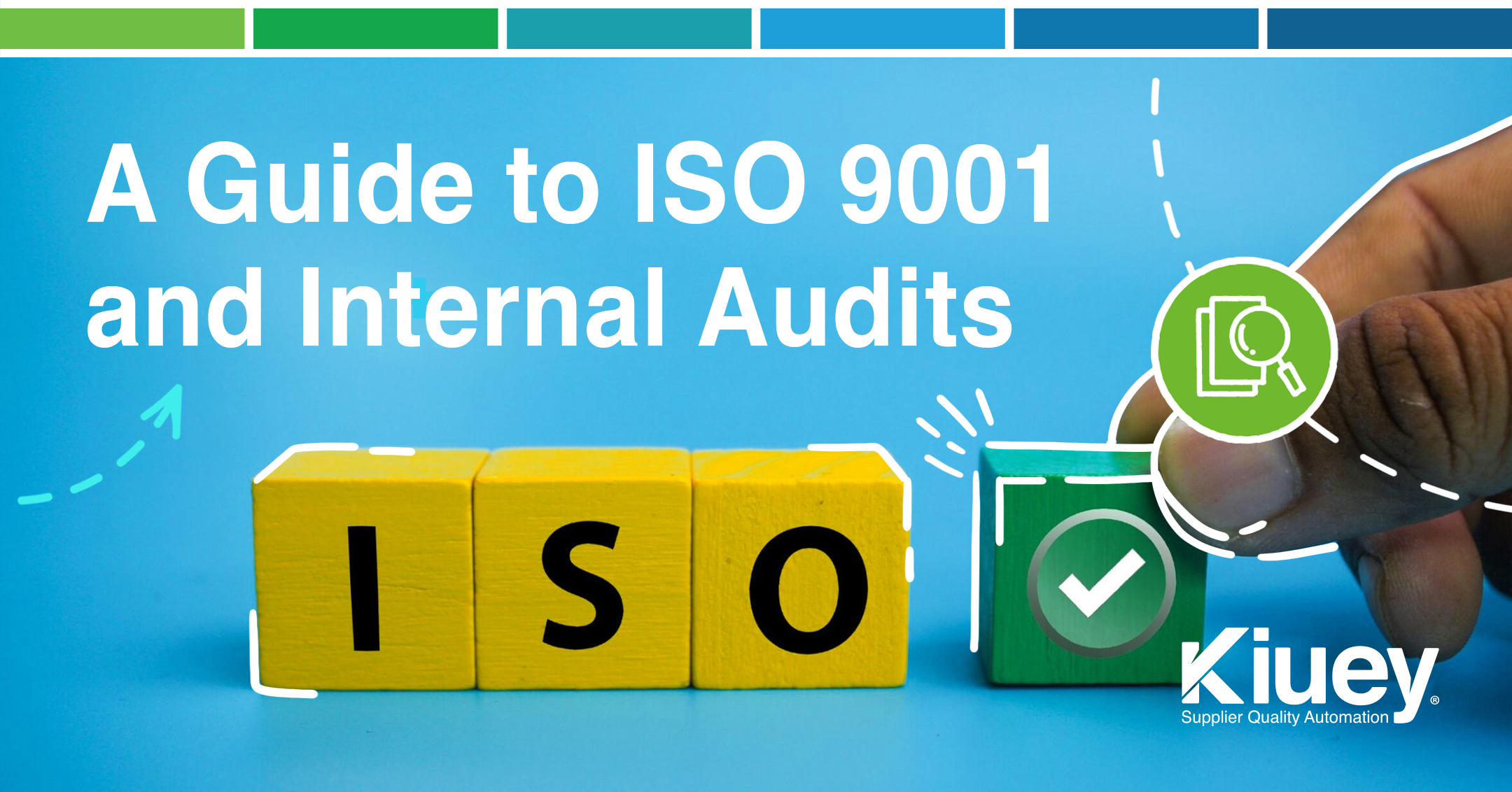
Over a million organizations worldwide trust the ISO 9001 Quality Management System (QMS) to achieve consistent success. This globally recognized standard helps businesses deliver products and services that consistently meet customer expectations, ultimately driving satisfaction and loyalty. ISO 9001’s versatility is a key strength – it can be applied by any organization, regardless of size, industry, or product complexity.
The Pillars of ISO 9001
The framework of ISO 9001 rests on seven core quality management principles:
- Customer Focus: Putting customer needs at the heart of everything you do.
- Leadership Commitment: Strong leadership sets the direction and promotes a culture of quality.
- Engaged People: Empowering and motivating your workforce is essential for achieving quality.
- Process-Based Approach: Viewing your organization as a network of interconnected processes improves efficiency.
- Continuous Improvement: Striving for ongoing betterment is key to long-term success.
- Data-Driven Decisions: Making informed choices based on accurate information.
- Relationship Management: Building strong partnerships with suppliers and other stakeholders.
When implementing a QMS, organizations should integrate these principles seamlessly into their business goals. An effective Business Operating System (BOS) can be a valuable tool for deployment.
ISO 9001 emphasizes strong leadership and promotes QMS adoption as a strategic decision that drives sustained organizational growth.
Why Choose ISO 9001?
The benefits of implementing ISO 9001 are numerous:
- Enhanced Performance: Improved efficiency and effectiveness across all areas of the organization.
- Increased Customer Satisfaction: Delivering products and services that consistently meet customer expectations.
- Streamlined QMS: Integrating the QMS into your overall Business Management System (BMS).
- Strategic Alignment: Aligning quality initiatives with your organization’s strategic direction.
- Effective Management Tools: Utilizing tools like process mapping, risk assessment, internal audits, and improvement processes.
By effectively implementing a QMS based on ISO 9001, organizations significantly increase their chances of achieving business goals. The standard’s requirements leverage management tools to demonstrate sustainable growth. These tools include process approach, risk-based thinking, internal audits, improvement processes, and management reviews.
Internal Audits: Ensuring QMS Effectiveness
Internal audits are a critical component of evaluating QMS performance and conformance. They involve gathering evidence to determine if the implemented QMS aligns with ISO 9001 requirements. This evidence is then analyzed to assess the extent to which audit criteria are met. Effective internal audits are conducted objectively, impartially, and utilize a well-defined audit program. Imagine an internal auditor as a physician examining the health of the QMS, rather than a police officer searching for faults.
The Power of Internal Audits
Regular internal audits offer valuable opportunities for improvement by identifying areas for corrective action and non-conformities. Top management should leverage the audit process to review the effectiveness of the implemented system and take necessary steps to achieve performance goals.
A well-executed internal audit program delivers a range of benefits, including:
- Improved Systems: Identifying areas for improvement and streamlining processes.
- Cost Reduction: Uncovering opportunities to save money through process optimization.
- Process Optimization: Fine-tuning processes for maximum efficiency and effectiveness.
Organizations can choose process-based audits to assess implemented systems, or result-oriented process audits to evaluate manufacturing or service delivery processes. Regardless of the chosen approach, effective internal audits contribute significantly to achieving organizational goals. Audit criteria can even be integrated with business goals and value-added activities to positively impact the bottom line.
The combination of ISO 9001 QMS and a robust internal audit process can propel organizations towards significant improvement, competitive advantage, and sustainable growth.
Subscribe to our newsletter.
Your go-to destination for insights, best practices, and innovative solutions in supplier quality assurance.
Recent Posts
How Kiuey simplifies PPAP and APQP compliance
August 21, 2025
AIAG vs VDA AIAG PFMEA? Know the differences between
July 23, 2025
Categories
Let's talk to see how PPAP Manager can help your company to save time and money.