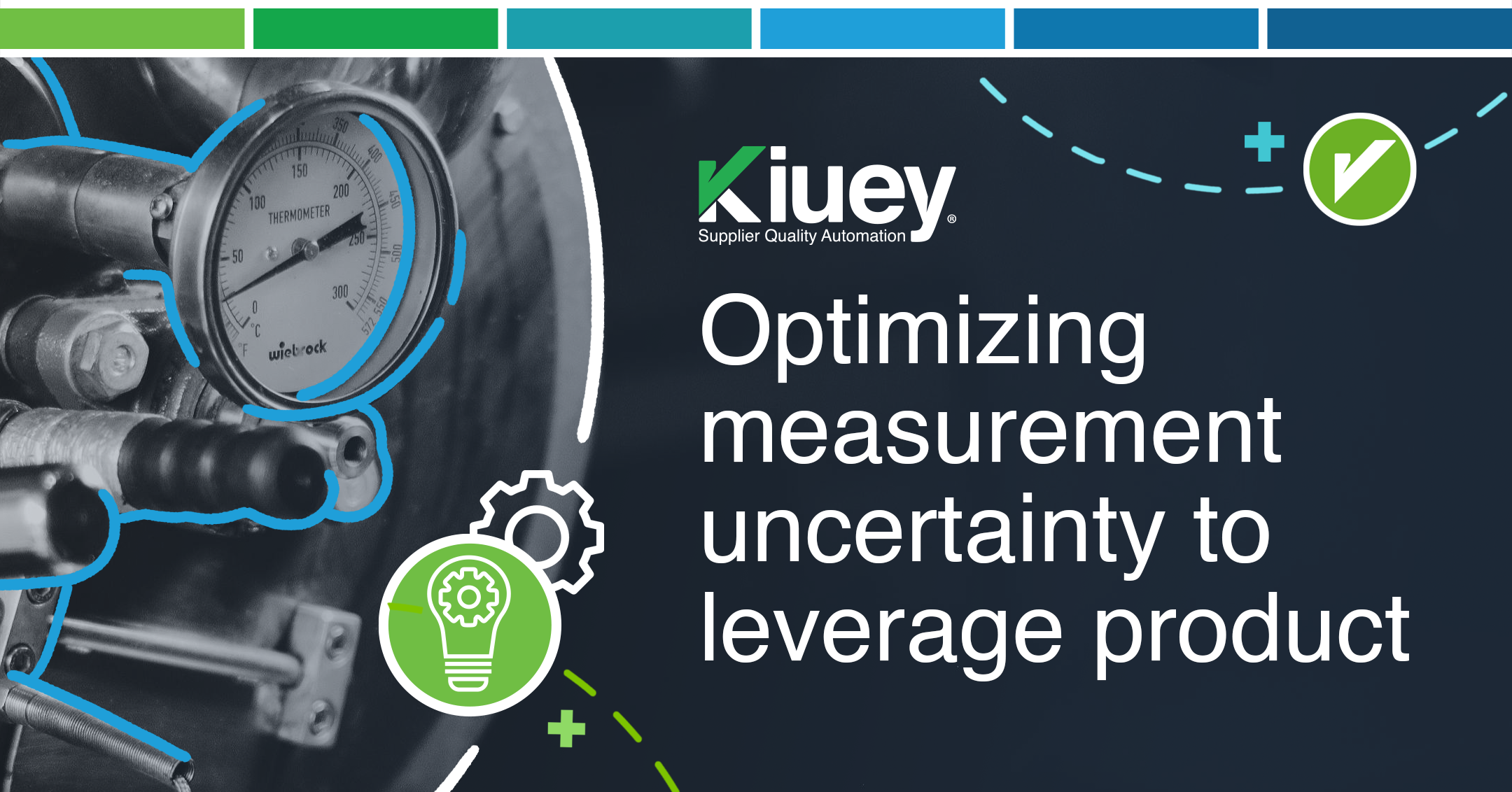
Optimizing Measurement Uncertainty for Enhanced Product Quality
Measurement uncertainty, a fundamental concept in quality control, is the range within which the true value of a measurement is expected to lie. While it’s impossible to eliminate measurement uncertainty completely, it can be minimized through various strategies to enhance product quality.
Measurement Uncertainty: What to do
Selecting Appropriate Measurement Equipment
The foundation of accurate measurements lies in the selection of suitable equipment. Instruments with high precision, meaning they produce consistent results within a narrow range, and accuracy, meaning they provide measurements that are close to the true value, are essential. Regular calibration of these instruments ensures their continued accuracy and reduces systematic errors.
Standardizing Measurement Procedures
Clear and standardized measurement procedures are crucial for consistency. Developing detailed protocols and providing comprehensive training to operators help minimize operator-related errors and ensure that measurements are performed consistently across the organization.
Controlling Environmental Factors
Environmental conditions can significantly impact measurement accuracy. Maintaining a stable temperature environment prevents variations due to thermal expansion or contraction, while controlling humidity levels avoids moisture-related issues. Additionally, minimizing vibrations helps ensure the stability of measurement instruments.
Reducing Sample Variability
To obtain representative and reliable measurements, it is essential to select samples that accurately represent the entire production batch. Increasing sample size can also improve statistical confidence and reduce random errors.
Using Statistical Methods
Statistical methods, such as control charts and gauge R&R studies, are invaluable tools for monitoring process variation and assessing the variation introduced by measurement systems. Control charts help identify trends that may indicate quality issues, while gauge R&R studies evaluate the repeatability and reproducibility of measurement systems.
Continuous Improvement
Continuous improvement is essential for optimizing measurement uncertainty. Regularly analyzing measurement data, identifying areas for improvement, and implementing corrective actions can help reduce errors and enhance product quality. Additionally, investigating the root causes of measurement errors can prevent recurrence and improve overall process efficiency.
Leveraging Technology
Advancements in technology offer opportunities for improving measurement accuracy and efficiency. Automation can reduce human error and improve consistency, while advanced measurement techniques, such as laser interferometry or 3D scanning, can provide higher precision and accuracy.
Conclusion
By carefully considering these factors and implementing effective strategies, manufacturers can optimize measurement uncertainty and significantly enhance product quality. This ultimately leads to increased customer satisfaction, reduced costs, and improved overall business performance. By prioritizing measurement accuracy and precision, organizations can ensure that their products meet the highest standards of quality.
Subscribe to our newsletter.
Your go-to destination for insights, best practices, and innovative solutions in supplier quality assurance.
Recent Posts
What is SCAR in quality management and how to handle it?
April 10, 2025
Categories
Let's talk to see how PPAP Manager can help your company to save time and money.