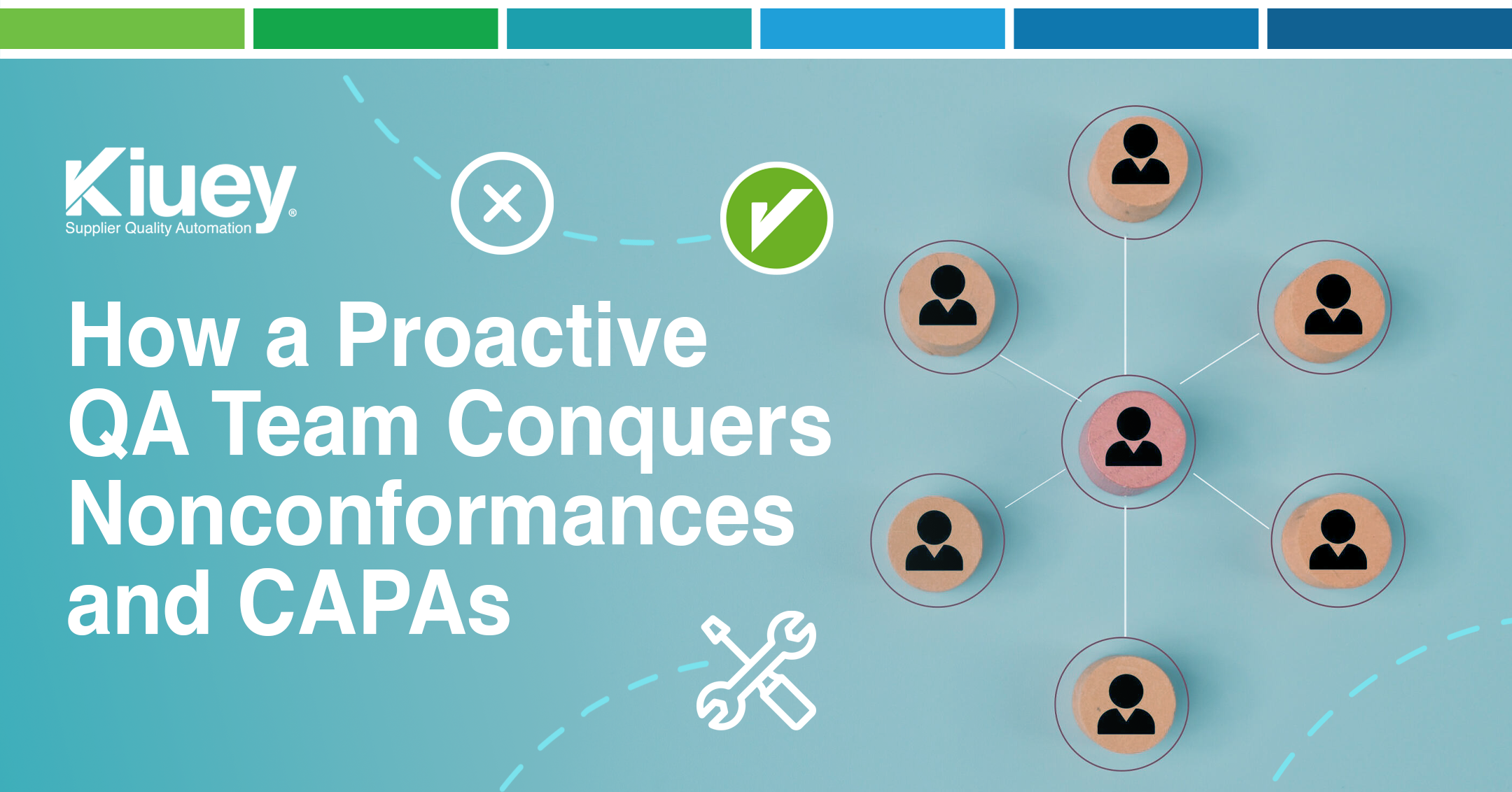
The Power of Engagement: How a Proactive QA Team Conquers Nonconformances and CAPAs
In the world of manufacturing, quality is everything. Even minor deviations from specifications, known as nonconformances, can have a ripple effect, impacting product safety, functionality, and ultimately, customer satisfaction. This is where a highly engaged Quality Assurance (QA) team steps in.
The Challenge of Nonconformances
Nonconformances can arise at various stages of production due to human error, material defects, or equipment malfunctions. Identifying and addressing these issues promptly is crucial. A disengaged QA team might simply document the nonconformance and move on. But a truly engaged team delves deeper.
The Engaged QA Advantage
An engaged QA team takes ownership of quality. They are proactive, solution-oriented, and view nonconformances as opportunities for improvement. Here’s how such a team tackles nonconformances and Corrective Action and Preventive Action (CAPA) processes:
- Early Detection: They go beyond final inspections and implement robust in-process checks. This allows for catching nonconformances early, minimizing rework and scrap.
- Root Cause Analysis (RCA): Engaged QA teams don’t just identify the nonconformance; they delve into the ‘why’ behind it. They use tools like fishbone diagrams and 5 Whys to identify the root cause, be it a design flaw, supplier issue, or a training gap.
- Effective CAPA Development: They don’t just create CAPAs; they craft effective ones. They ensure CAPAs are specific, measurable, achievable, relevant, and time-bound (SMART). They involve relevant personnel from production, engineering, and procurement in CAPA development, fostering a sense of ownership.
- Communication and Collaboration: They keep all stakeholders informed. This includes clear communication with production about the nonconformance and the implemented corrective actions. They collaborate with other departments to ensure preventive actions are effectively implemented.
- Verification and Validation: Engaged QA teams don’t just assign CAPAs; they verify their effectiveness. They monitor the implementation of corrective actions and conduct follow-up inspections to ensure the preventive actions are working. They use data analysis to track trends and identify areas for improvement in the QA process.
The Benefits of a Proactive Approach
The impact of a highly engaged QA team goes beyond just resolving non-conformances. Here are some of the key benefits:
- Reduced Costs: Early detection and effective CAPAs minimize rework and scrap, leading to significant cost savings.
- Improved Quality: Proactive identification and resolution of nonconformances lead to a consistent and higher quality of manufactured products.
- Enhanced Customer Satisfaction: Consistent quality translates to a better customer experience, fostering loyalty and trust.
- Continuous Improvement: By analyzing nonconformances and CAPA trends, engaged QA teams to identify areas for improvement in the manufacturing process, leading to a culture of constant improvement.
Fostering Engagement
So how do you create a culture of engagement within your QA team? Here are some key strategies:
- Invest in Training: Provide training on nonconformance identification, RCA techniques, and CAPA development. Encourage participation in industry conferences and workshops.
- Empowerment: Give QA team members the authority to make decisions and take ownership of quality issues.
- Recognition and Rewards: Recognize and reward team members who identify and effectively resolve nonconformances. Celebrate successes and milestones.
- Open Communication: Foster a culture of open communication where team members feel comfortable raising concerns and suggesting improvements.
Conclusion
In today’s competitive manufacturing landscape, a highly engaged QA team is not a luxury; it’s a necessity. By proactively identifying and resolving nonconformances and implementing effective CAPAs, an engaged QA team can ensure consistent quality, reduce costs, and ultimately, contribute to the entire organization’s success.
Subscribe to our newsletter.
Your go-to destination for insights, best practices, and innovative solutions in supplier quality assurance.
Recent Posts
What is SCAR in quality management and how to handle it?
April 10, 2025
Categories
Let's talk to see how PPAP Manager can help your company to save time and money.