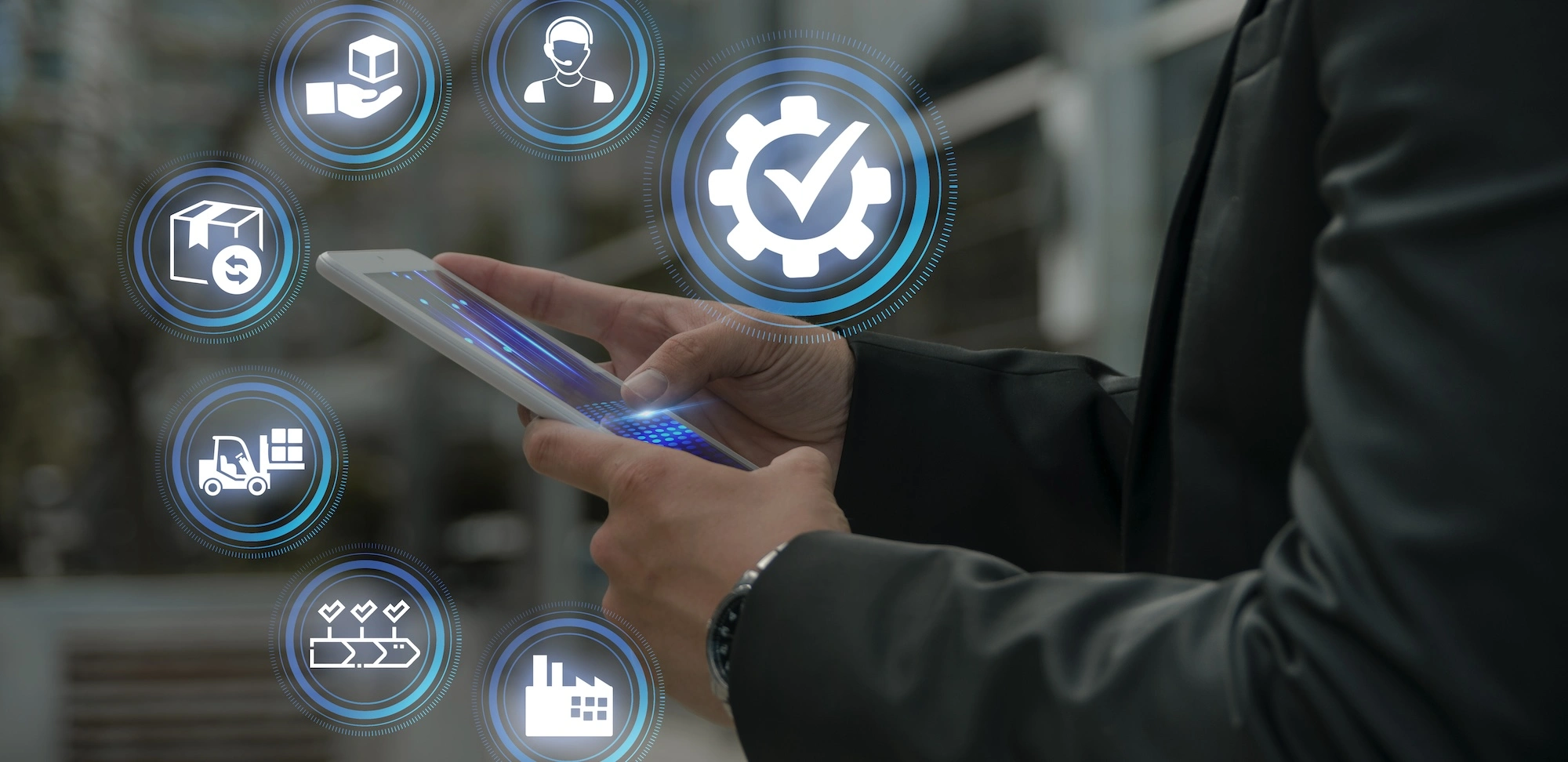
The quality engineer’s guide to effective problem-solving
Quality engineers are always on the lookout for problems that need fixing. In the quality management field, challenges can arise at any stage —from production hiccups to process inefficiencies—, and it’s a SQE’s job to identify and methodically solve them.
To ensure excellence and reliability, quality engineer problem-solving involves complex examination techniques like root cause analysis and the CAPA process, and applies powerful quality management frameworks like the 8D methodology and Six Sigma. By mastering these fundamental problem-solving techniques, quality engineers can tackle issues with precision and drive excellence through actionable solutions.
This guide delves into the core aspects of quality engineer problem-solving, offering insights into proven methodologies and real-world applications. Keep reading to learn more and broaden your expertise as a problem-solving leader in the field.
Why problem-solving is critical in quality engineering
The complexity of modern manufacturing systems and supply chain management make problem-solving a critical skill to address quality engineering issues effectively.
Due to its direct impact on product condition, efficiency, fabrication cost and market success, manufacturing errors can lead to costly rework, production delays, customer dissatisfaction and non-compliance with industry standards. Structured problem-solving techniques enable quality engineers to identify, analyze, and rectify issues, thus ensuring product quality, process efficiency, risk prevention and regulatory compliance.
Integrating advanced technologies to streamline processes, such as PPAP/APQP and SCAR/CAPA management software, further enhances a quality engineer’s problem-solving capabilities. This systematic approach allows more precise and efficient solutions.
The 5 key steps in quality engineering problem-solving
This section breaks down the five essential steps for quality engineer problem-solving. From identifying the root cause to implementing corrective and preventive actions, and monitoring the effectiveness of the solution, here’s what you need to know:
Step 1 – Identifying the problem accurately
Upon arising difficulties, the first thing to do is understand the problem: what is it, who does it involve, where did it happen, when did it happen, and why.
Thoroughly document how processes currently operate in a written report. Analyze your findings and review existing data to further comprehend the origin, nature, impact, and scope of the quality issue. Look for evidence that reveals underlying causes rather than focusing on symptoms, personal intuition or people’s opinions.
Step 2 – Performing a Root Cause Analysis
The Root Cause Analysis (RCA) involves a wide scope of problem-solving techniques, methods and tools applied for pinpointing the real cause of a non-conformance or quality problem. A “root cause” can be defined as the precise mark in the causal chain that originates the issue. This is where implementing corrective action can prevent the problem from happening.
Step 3 – Implementing Corrective and Preventive Actions (CAPA)
Corrective and preventive action (also known as CAPA) is a quality management strategy used for addressing and resolving identified non-conformities. It reduces risks in the workplace, avoids production defects and improves manufacturing overall.
According to the Automotive Industry Action Group (AIAG), corrective and preventive action refers to “Any action taken by an organization that is designed to permanently prevent the reoccurrence of the failure mode, detect when the failure mode or effect occurs, and to plan for the failure mode and its risks”.
Step 4 – Monitoring and verifying the solution
Quality engineer problem-solving is only effective as long as the solution remains in place, so the QA team is responsible for making sure none of the reported flaws reoccur after the implementation of the corresponding corrective and preventive actions.
Monitoring and verifying the solution also implies being on the lookout for any new developments that may take place, such as new errors that may indicate:
- Poorly executed fixing measurements
- Wrong solution design
- Mistaken root cause
Step 5 – Continuous improvement and prevention
Remember, quality management is an ongoing process. Solutions need to be constantly refined as industries evolve, organizations change, and clients’ needs transform.
While understanding the importance of the CAPA process, Root Cause Analysis, and other problem-solving techniques is fundamental to a quality engineer’s job, reflecting on the lessons drawn from the experience and future opportunities for improvement is what drives excellence. This entails keeping comprehensive documentation regarding all aspects of the manufacturing process, as a way of building historic data that’s useful for decision-making.
Tools and software to streamline problem-solving
When implementing a corrective and preventive actions plan, quality engineers often face obstacles such as lack of data transparency, resistance to change, and analysis paralysis. However, nowadays there are software tools that can significantly enhance problem-solving by improving cross-functional communication among the quality management processes.
Digital solutions can reduce repetitive manual work and improve data accuracy, while allowing quality engineers to focus on higher importance tasks with an assertive mindset.
This technology helps quality engineers to track and resolve issues faster, which streamlines problem-solving —imagine having automated workflows, AI-driven metrics and reports generated for you, derived from your process documentation input, all in the same portal!
Kiuey offers a flexible and on-demand software solution for all your quality management needs, from the PPAP and APQP approval process to kicking-off SCARs and tracking their status. Schedule a demo and start saving up to 50% of time and resources!
Subscribe to our newsletter.
Your go-to destination for insights, best practices, and innovative solutions in supplier quality assurance.
Recent Posts
How Kiuey simplifies PPAP and APQP compliance
August 21, 2025
AIAG vs VDA AIAG PFMEA? Know the differences between
July 23, 2025
Categories
Let's talk to see how PPAP Manager can help your company to save time and money.