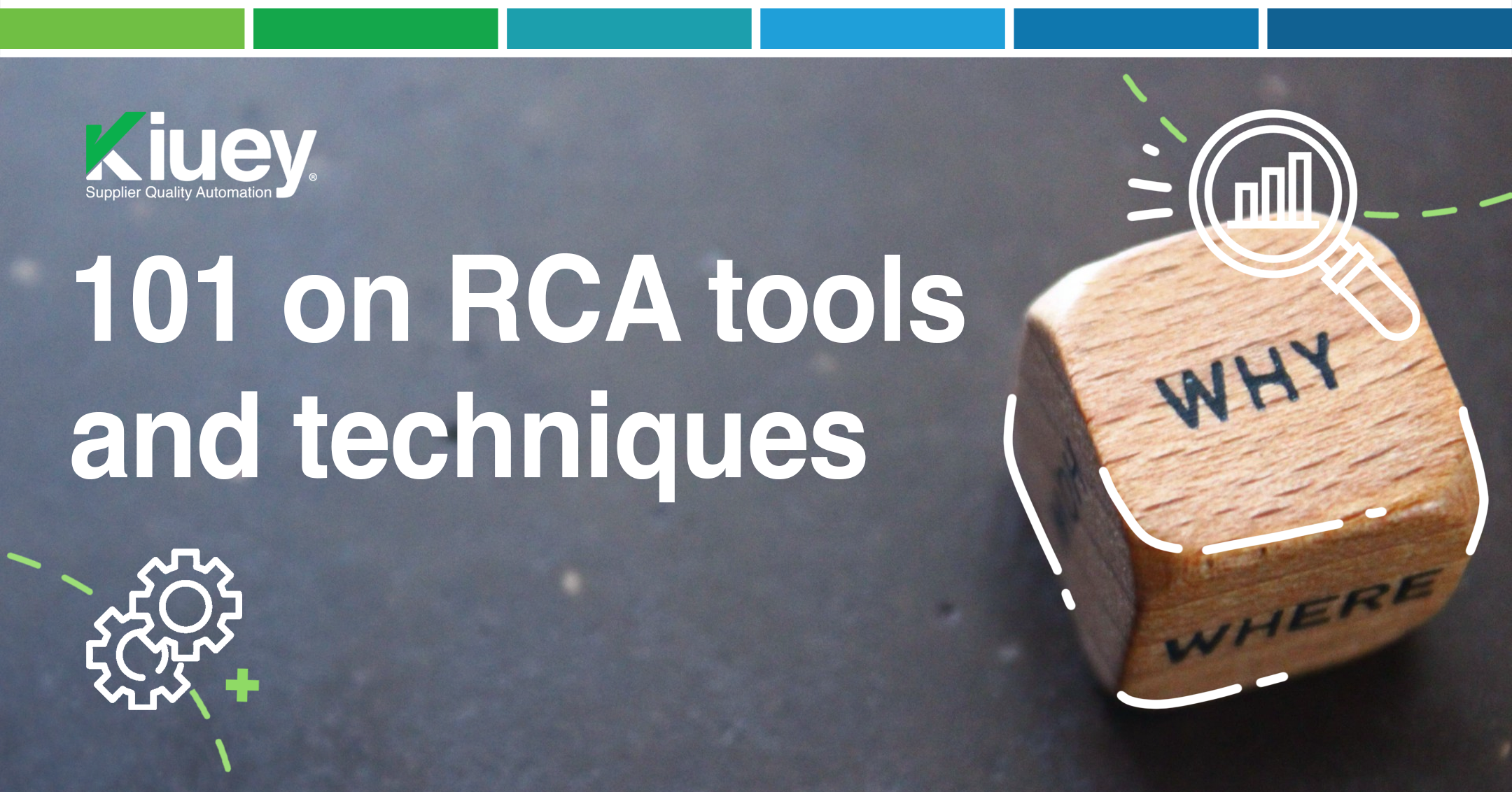
In the fast-paced world of manufacturing, critical quality and efficiency are essential for success. However, unexpected issues and production roadblocks can disrupt operations and impact the bottom line. To achieve long-term success, manufacturers need to go beyond simply fixing problems; they need to identify the root cause to prevent them from recurring. This is where Root Cause Analysis (RCA) comes in.
RCA, a systematic approach for production issues
RCA is a systematic approach for pinpointing the underlying reasons behind quality deviations and production problems. By delving deeper than just the symptoms, manufacturers can implement corrective actions that address the true source of the issue, ultimately preventing similar occurrences in the future. This proactive approach fosters continuous improvement, leading to enhanced product quality, reduced waste, and increased overall efficiency.
Several powerful RCA tools are available to manufacturing teams, each offering a unique approach to problem-solving. Let’s explore some of the most valuable:
1. The 5 Whys: A Straightforward Path to the Root
Simple yet impactful, the 5 Whys technique encourages a structured and iterative questioning process. Essentially, you begin by asking “why” the problem is happening and then continue asking “why” in response to each answer you receive. This repetitive questioning helps peel back the layers, uncovering the root cause beneath the surface symptoms.
For instance, if a machine is producing defective parts, the initial question might be: “Why are the parts defective?” The answer could be: “Because the machine settings are incorrect.” The next “why” would be: “Why are the settings incorrect?” This process continues until you reach a fundamental cause, such as: “Because the procedures weren’t clear or up-to-date, leading to operator error.”
The 5 Whys is a versatile tool applicable to a wide range of manufacturing issues. Its strength lies in its simplicity and ability to guide a team towards a clear understanding of the root cause.
2. Fishbone Diagram (Ishikawa Diagram): Unveiling a Multifaceted Problem
The Fishbone Diagram, also known as the Ishikawa Diagram, provides a visual framework to explore all the potential contributing factors to a problem. Shaped like a fish skeleton, the main problem sits at the head. Branches stemming from the spine represent various categories that might influence the issue, such as: People, Machines, Materials, Methods, Measurement, and Environment (MMMEEM).
Team members brainstorm potential causes within each category. For example, under “People,” factors like inadequate training or operator fatigue could be listed. By systematically examining all these possibilities, the team can gain a comprehensive picture of the potential root causes.
The Fishbone Diagram’s strength lies in its ability to stimulate comprehensive thinking and prevent overlooking crucial factors. It fosters collaboration and ensures all potential causes are considered before pinpointing the root.
3. Pareto Chart (80/20 Rule): Prioritizing the Most Impactful Causes
The Pareto Chart, often referred to as the 80/20 rule, focuses on identifying the most significant factors contributing to a problem. This principle suggests that roughly 80% of the effects (problems) stem from 20% of the causes.
By plotting the frequency of different potential causes identified through other RCA tools (like the Fishbone Diagram), the Pareto Chart reveals which factors have the most significant impact. This allows teams to prioritize their efforts, focusing on addressing the 20% of causes responsible for the majority of the issues.
The Pareto Chart is a valuable tool for optimizing resource allocation. By directing efforts towards the most impactful factors, manufacturers can achieve significant improvements with targeted actions.
4. Failure Mode and Effects Analysis (FMEA): Proactive Problem Prevention
FMEA takes a proactive approach to RCA. This technique involves systematically identifying potential failure modes within a process, analyzing the risks associated with each failure, and implementing preventive measures to mitigate them before they occur.
By proactively identifying potential problems, FMEA allows manufacturers to establish preventative measures and safeguards. This not only reduces the likelihood of issues arising but also minimizes the impact if a failure does occur. FMEA is particularly valuable for complex processes with multiple potential failure points.
Conclusion: A Robust RCA Toolkit for Manufacturing Excellence
These RCA tools, along with others like Cause and Effect Diagrams and Scatter Plots, equip manufacturing teams with a powerful arsenal for problem-solving. By effectively utilizing these techniques, manufacturers can move beyond simply addressing symptoms and delve deeper to identify the root cause of quality issues and production problems.
Implementing a structured RCA process fosters continuous improvement within a manufacturing environment. Through RCA, manufacturers can achieve greater efficiency, reduce waste, enhance product quality, and ultimately gain a significant competitive advantage.
Subscribe to our newsletter.
Your go-to destination for insights, best practices, and innovative solutions in supplier quality assurance.
Recent Posts
How Kiuey simplifies PPAP and APQP compliance
August 21, 2025
AIAG vs VDA AIAG PFMEA? Know the differences between
July 23, 2025
Categories
Let's talk to see how PPAP Manager can help your company to save time and money.