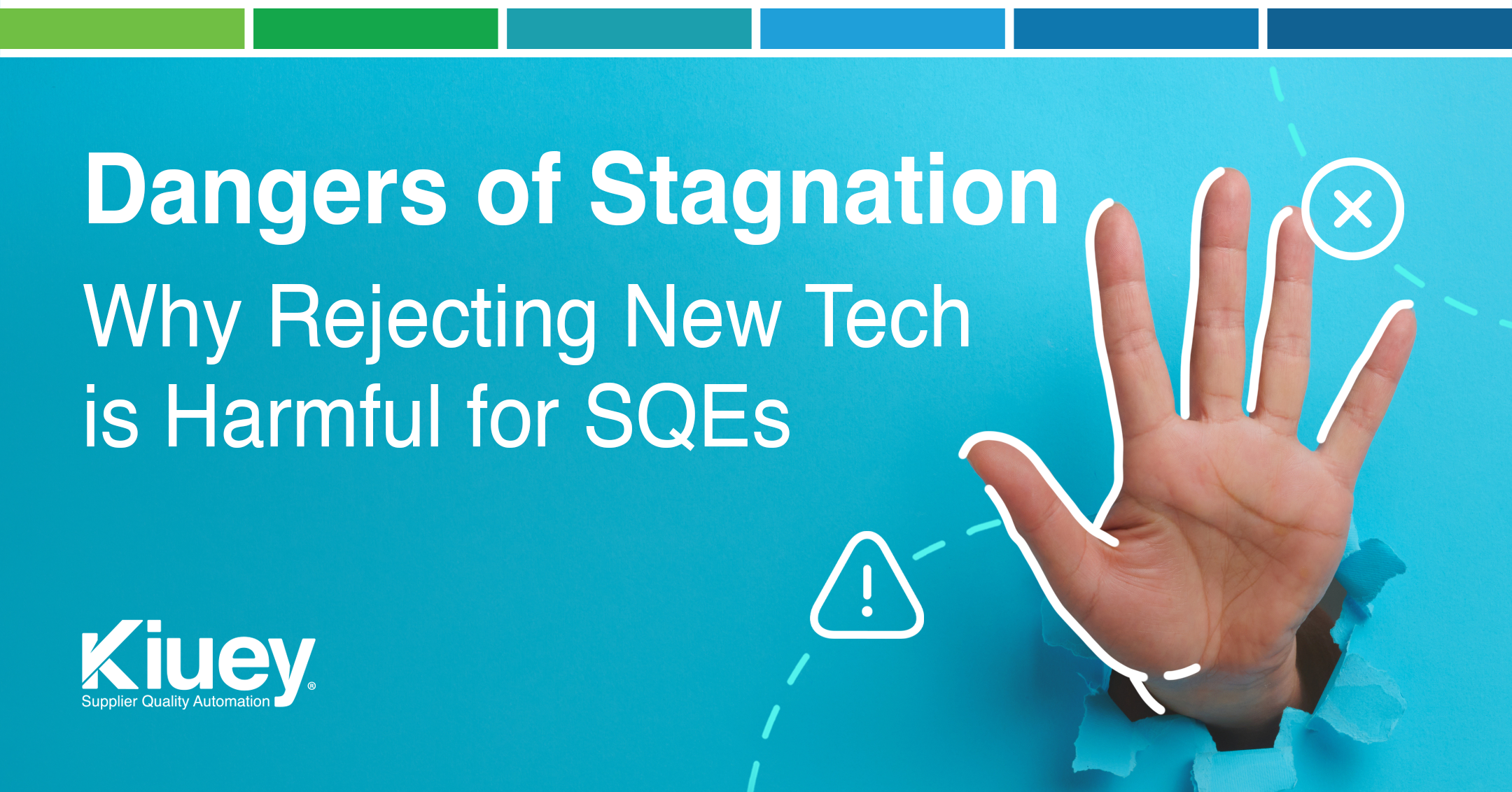
The frustration crackled in Sarah’s voice as she slammed her laptop shut. “This new system is a nightmare,” she grumbled to her colleague, David. Sarah, a seasoned Supplier Quality Engineer (SQE), had spent the morning wrestling with a recently implemented quality management platform.
Does that short story sounds familiar to you? The relentless march of technology impacts every facet of business, and quality management is no exception. New tools and platforms are constantly emerging to streamline processes, improve data analysis, and enhance supplier collaboration. Yet, seasoned SQEs like Sarah – the gatekeepers of quality at the supplier interface – can be surprisingly hesitant to embrace these advancements.
Understanding the reasons behind this resistance is crucial for successful technology adoption within the supplier quality function. Here, we explore some of the key roadblocks:
- Fear of the Unknown: SQEs often develop a strong foundation in established methods. Transitioning to a new platform, with unfamiliar interfaces and workflows, can feel daunting. The fear of making mistakes or jeopardizing established quality control systems can lead to a reluctance to embrace change.
- Time Constraints: Integrating new technology requires learning and adaptation. This can be a significant time investment, especially for SQEs already burdened with daily quality management tasks. The perceived lack of time for training or exploration can discourage them from venturing into uncharted technological territory.
- Skill Gaps: New technologies often demand different skillsets. If SQEs lack the necessary technical background or training to utilize the new platform effectively, it can further amplify their resistance. Feeling underprepared can lead to frustration and a desire to stick with the familiar.
- Lack of Perceived Value: Not every new technology clearly translates to tangible benefits. SQEs might struggle to see how the new platform will improve their existing workflows. A lack of clear communication regarding the benefits of the technology can hinder their motivation to adopt it.
- Integration Challenges: New technologies need to seamlessly integrate with existing quality management systems (QMS) for optimal efficiency. Integration issues can lead to data silos and duplication of effort. SQEs might resist a technology if it complicates their current workflows instead of streamlining them.
Breaking Down the Barriers: Strategies for Successful New Technology Adoption
Fortunately, there are strategies to overcome these hurdles and encourage SQE adoption of new technology:
- Emphasize Benefits: Clearly communicate the advantages of the new technology, showcasing how it will save time, improve data analysis, or enhance communication with suppliers. Highlight real-world examples and success stories to pique their interest.
- Invest in Training: Provide comprehensive training designed specifically for SQEs. Tailor the training to address their concerns and ensure they feel confident navigating the new platform.
- Promote Continuous Learning: Encourage a culture of continuous learning within the team. Offer ongoing support and resources to keep SQEs updated on the latest functionalities and best practices.
- Address Concerns: Actively listen to SQE concerns regarding the new technology. Address their fears and skill gaps head-on. Offer tailored support and mentorship to ease the transition.
- User-Friendly Technology: Choose technology that is intuitive and user-friendly. A platform with a clear interface and readily available help features can significantly reduce the learning curve for SQEs.
- Data Integration: Ensure smooth integration between the new technology and existing QMS. Streamline data flow and avoid the creation of data silos that can hinder efficiency.
Building a Future-proof Quality Function
By understanding the root causes of resistance and implementing effective adoption strategies, organizations can empower their SQEs to leverage the power of new technologies. A tech-savvy supplier quality function can optimize processes, improve communication, and ultimately deliver superior quality products and services. In today’s rapidly evolving technological landscape, fostering a culture of continuous learning and adaptation is no longer a choice, it’s a necessity for a future-proof supplier quality function.
While the initial discomfort of adapting to new technology is understandable, the long-term consequences of sticking with outdated methods can be significant. Here’s why embracing new tech is crucial for SQEs:
- Falling Behind the Curve: The quality landscape is constantly evolving. New technologies like AI-powered risk assessments and real-time data analytics can provide a significant edge. By clinging to traditional methods, SQEs risk falling behind competitors who leverage these advancements for better supplier performance and risk mitigation.
- Inefficiency and Errors: Manual, paper-based processes are prone to errors and inefficiencies. New technologies can automate tedious tasks, freeing up valuable time for SQEs to focus on strategic initiatives. Additionally, data-driven insights from these platforms can help identify quality issues early on, preventing costly product recalls or delays.
- Communication Silos: Outdated communication methods like email chains can lead to miscommunication and delays. Collaboration platforms integrated with new quality management systems can streamline communication with suppliers, ensuring everyone is on the same page.
- Limited Visibility: Traditional methods often lack the ability to provide real-time visibility into supplier performance. Advanced technologies can offer comprehensive dashboards and reporting tools, giving SQEs a holistic view of supplier quality across the entire supply chain.
- Loss of Competitive Advantage: In today’s competitive market, companies that embrace innovation and utilize technology effectively gain a significant edge. SQEs who resist new technologies risk jeopardizing their company’s ability to deliver high-quality products and services.
By actively participating in the adoption of new technologies, SQEs can transform themselves from quality gatekeepers into strategic partners, driving continuous improvement throughout the supply chain.
Subscribe to our newsletter.
Your go-to destination for insights, best practices, and innovative solutions in supplier quality assurance.
Recent Posts
How Kiuey simplifies PPAP and APQP compliance
August 21, 2025
AIAG vs VDA AIAG PFMEA? Know the differences between
July 23, 2025
Categories
Let's talk to see how PPAP Manager can help your company to save time and money.