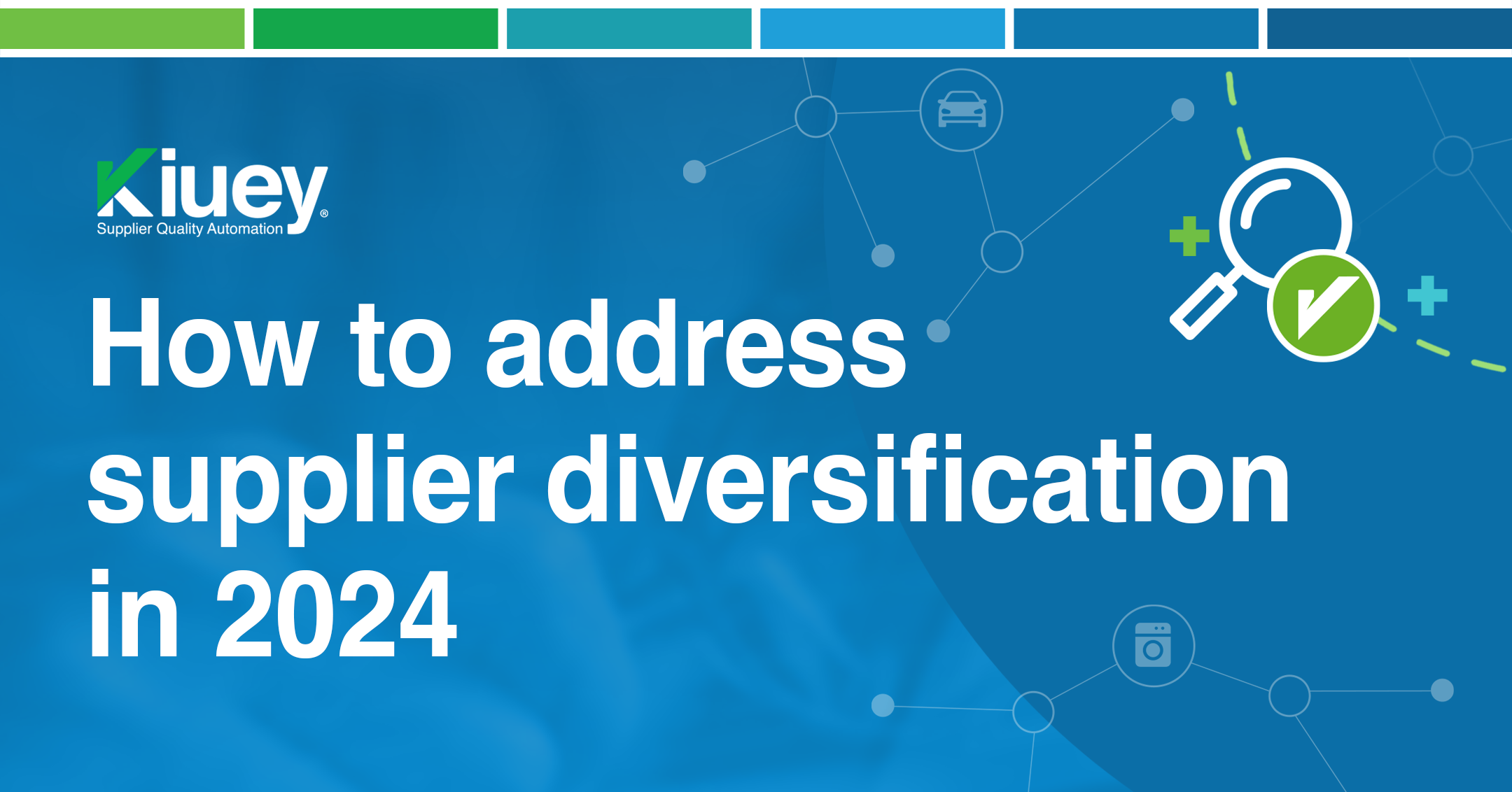
How to address supplier diversification in 2024
Supplier diversification is a strategic decision that can significantly impact supply chain resilience and risk mitigation. A Supplier Quality Engineer plays a crucial role in this process by ensuring that new suppliers meet the same stringent quality standards as existing ones.
Here’s how a Supplier Quality Engineer can address supplier diversification:
1. Supplier Qualification and Assessment:
- Develop robust qualification criteria: Create clear and comprehensive standards for evaluating potential suppliers, including quality systems, process capabilities, and performance metrics.
- Conduct thorough assessments: Implement a rigorous supplier qualification process involving on-site audits, document reviews, and sample evaluation.
- Evaluate supplier performance history: Assess the track record of potential suppliers, including their quality performance, delivery reliability, and financial stability.
2. Quality System Implementation:
- Transfer quality standards: Ensure that quality standards, processes, and documentation are effectively transferred to new suppliers.
- Provide training and support: Offer training and technical assistance to help new suppliers implement and maintain required quality systems.
- Monitor and audit compliance: Conduct regular audits to verify that new suppliers are adhering to quality standards and implementing corrective actions as needed.
3. Risk Assessment and Mitigation:
- Identify potential risks: Analyze the potential risks associated with new suppliers, including supply chain disruptions, quality issues, and financial instability.
- Develop contingency plans: Create backup plans to mitigate risks and ensure business continuity in case of supply chain disruptions.
- Implement risk management strategies: Implement risk management strategies such as dual sourcing, inventory buffers, and supplier performance monitoring.
4. Supplier Development and Performance Management:
- Establish performance metrics: Define key performance indicators (KPIs) to measure supplier quality performance and identify areas for improvement.
- Provide feedback and coaching: Offer constructive feedback to new suppliers to help them improve their performance and address quality issues.
- Implement supplier development programs: Develop programs to help new suppliers enhance their capabilities and meet quality expectations.
5. Collaboration and Communication:
- Foster strong relationships: Build strong relationships with new suppliers based on trust, open communication, and collaboration.
- Share quality data: Share quality data and performance metrics with suppliers to promote transparency and continuous improvement.
- Involve suppliers in problem-solving: Collaborate with suppliers to identify and resolve quality issues through root cause analysis and corrective action.
By following these steps, a Supplier Quality Engineer can effectively manage the challenges associated with supplier diversification while ensuring that the company maintains high-quality standards.
Tags:
Subscribe to our newsletter.
Your go-to destination for insights, best practices, and innovative solutions in supplier quality assurance.
Recent Posts
Emerging technologies for quality control processes
June 24, 2025
PPAP management and how can Kiuey aid you
June 19, 2025
Categories
Let's talk to see how PPAP Manager can help your company to save time and money.