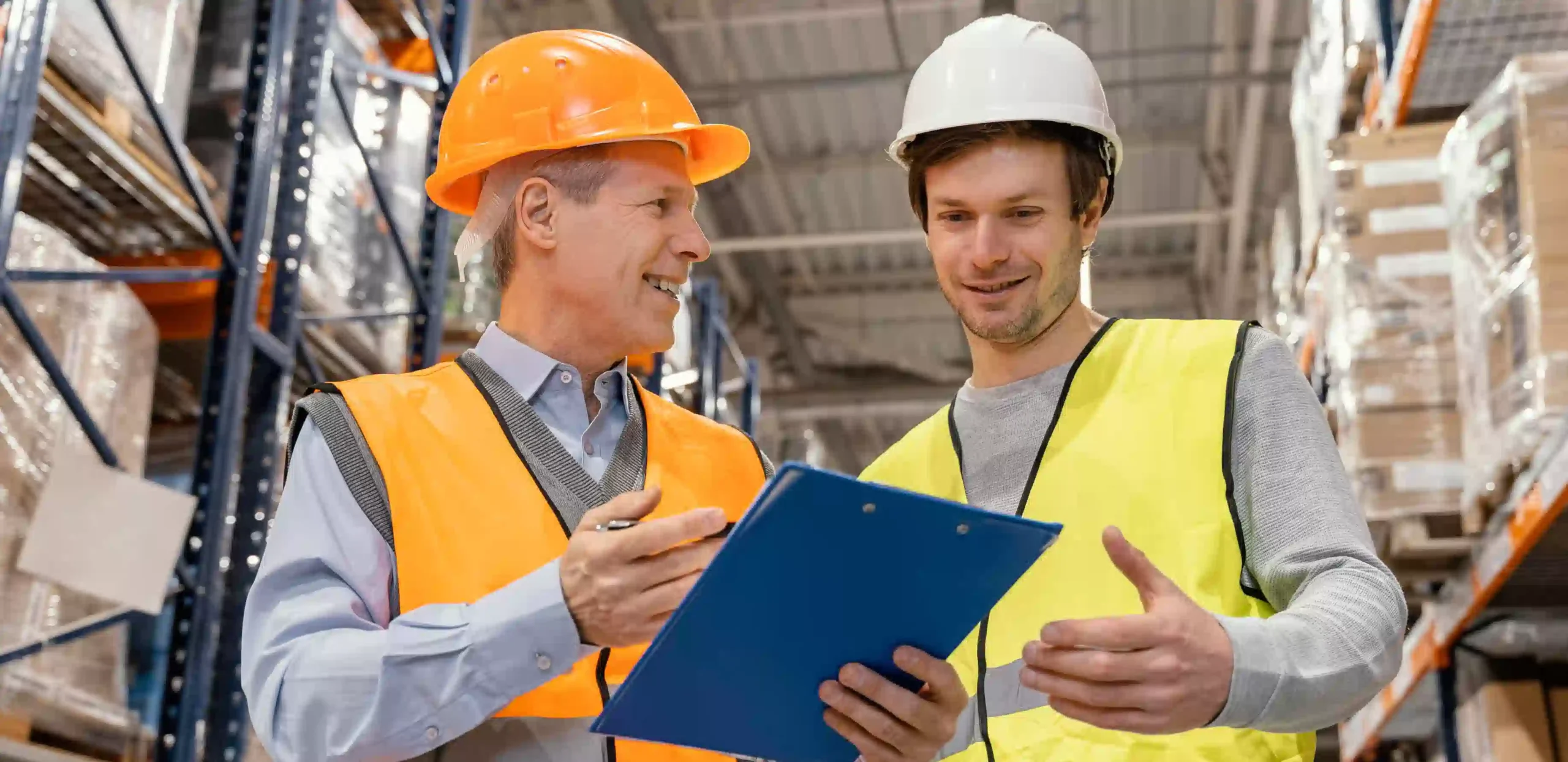
What is SCAR (Supplier Corrective Action Request) and why does it matter?
In the unpredictable field of quality management, relationships with suppliers are often as critical as the supply chain processes and products themselves. When issues arise —be it defects, delays, or nonconformities— the Supplier Corrective Action Request (SCAR) becomes a tool for collaboration towards quality assurance, and a pathway to excellence.
This approach strengthens the foundation of the supplier management process while ensuring quality standards, by not only resolving immediate challenges but also addressing the root causes of these problems, and guiding suppliers towards corrective measures.
Across industries, SCAR has proven its worth in improving supplier quality management, ensuring consistency, and driving innovation. Learn more about how you can transform challenges into opportunities for growth in your organization with SCAR, in this article.
What is SCAR?
A Supplier Corrective Action Request (SCAR) is a formal request issued to suppliers when their products or services fail to meet specified requirements, to address and rectify non-conformances. This document helps manufacturers make sure suppliers take necessary corrective actions to prevent recurrence of errors and improve quality management.
SCAR is integral to maintaining compliance with industry standards and regulations, thereby safeguarding product safety and customer satisfaction. It involves identifying the root cause of a problem, implementing corrective actions, and verifying their effectiveness.
Key elements of a high-quality SCAR
Issuing a SCAR means initiating a structured process that begins with the notification of nonconformity, and involves fundamental aspects such as investigation of root causes, development and implementation of corrective actions, and verification of effectiveness.
The fundamental aspects of a high-quality SCAR are:
- Problem identification and reporting: Non-conformances are identified through audits, inspections, or customer feedback, and a SCAR is issued to the supplier. Clearly define the problem, including detailed descriptions, defect data, and its impact.
- Root Cause Analysis: Suppliers are required to conduct a thorough investigation to determine the root cause of the issue, using tools like the 5 Whys technique or Fishbone diagrams to pinpoint the underlying causes.
- Corrective action implementation: Based on the analysis, develop a structured plan with immediate containment measures, long-term corrective actions, preventive strategies, and timelines. Identify and assign responsibilities accordingly.
- Validation and verification: Ensure the effectiveness of corrective actions through systematic validation. If no further issues arise and the corrective actions are verified, mark the problem as solved satisfactorily in your SCAR report.
- Documentation and continuous monitoring: Remember to maintain comprehensive records of all findings, decisions, and actions taken. Implement follow-up processes to track the sustained effectiveness of corrective actions.
These elements collectively ensure that SCARs are not only effective in resolving quality issues but also contribute to long-term improvements in supplier quality management.
Why SCAR quality matters
SCAR quality refers to the effectiveness and thoroughness of this process in identifying, addressing, and preventing quality issues. High-quality SCARs ensure that problem-solving leads to lasting solutions in supplier performance and overall supply chain reliability.
From start to finish, SCAR quality depends on detailed documentation and analysis, and the collaboration between suppliers and manufacturers. This makes for corrective actions that are not based on assumptions but are backed by data and thorough investigation.
Some organizations use software solutions to better manage this process, ensuring that all necessary information is properly captured and tracked in a comprehensive way.
Improve your supplier quality management process
The Supplier Corrective Action Request is a key component of Supplier Quality Management. At its heart, SCAR is about aligning with suppliers to achieve shared goals and elevate quality standards. However, handling SCARs through cumbersome spreadsheets, scattered emails, and inconsistent workflows can make this task difficult in practice.
Simplify the intricacies of the SCAR process with an automated and collaborative solution like our SCAR/CAPA Manager. Real-time reporting, automatic reminders and task management allow for easier collaboration with suppliers to identify and mitigate quality problems.
Save time and resources gathering all your supplier management process information in the same place. Try Kiuey’s software and discover a new way to ensure quality.
Subscribe to our newsletter.
Your go-to destination for insights, best practices, and innovative solutions in supplier quality assurance.
Recent Posts
How Kiuey simplifies PPAP and APQP compliance
August 21, 2025
AIAG vs VDA AIAG PFMEA? Know the differences between
July 23, 2025
Categories
Let's talk to see how PPAP Manager can help your company to save time and money.