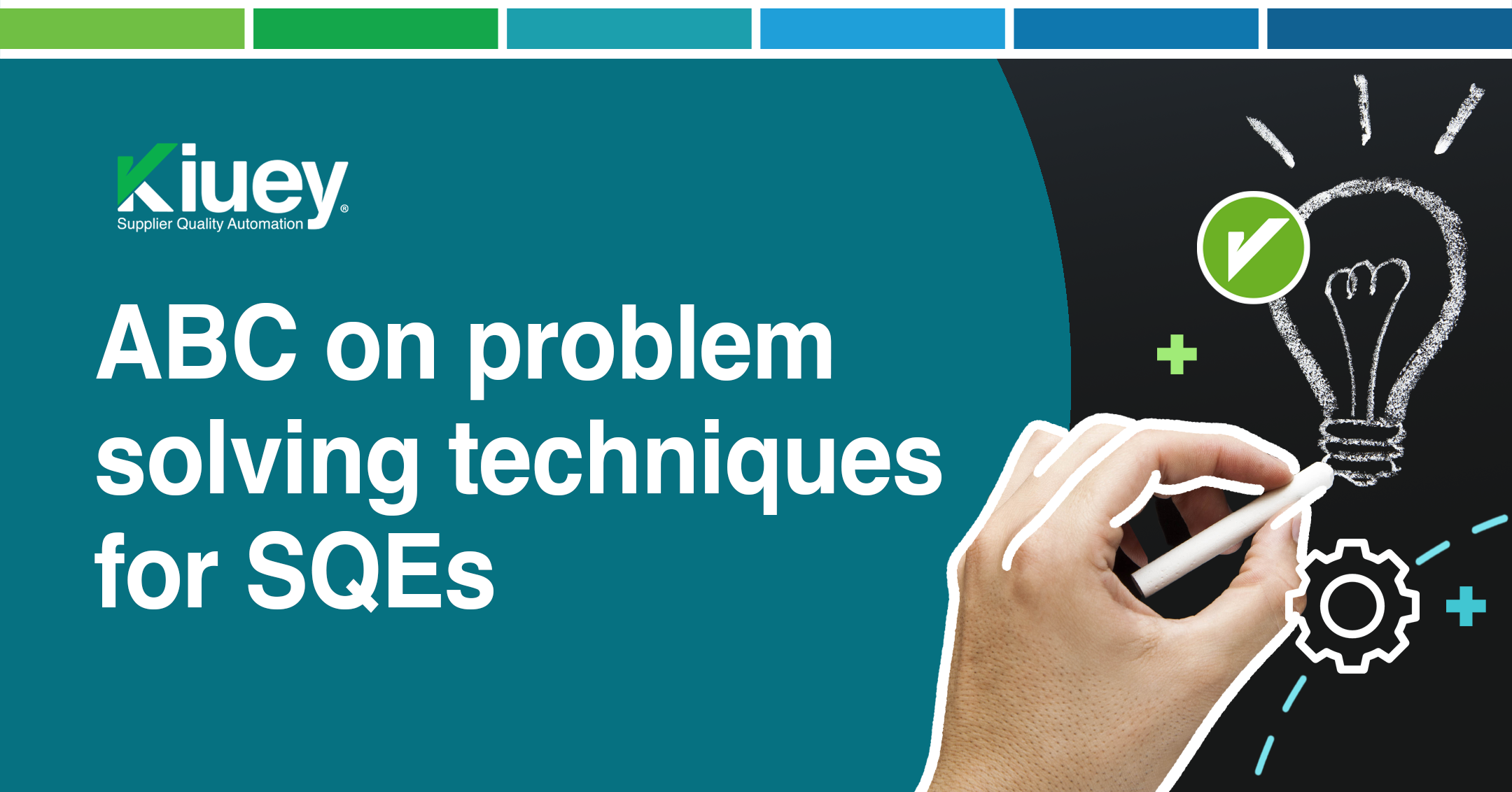
Supplier quality engineers play a crucial role in ensuring the quality of products and services delivered by suppliers. While technical skills are essential, soft skills are equally important in building strong relationships, fostering trust, and effectively addressing quality issues.
Key problem solving techniques integrated with soft skills
Empathetic Root Cause Analysis
By actively listening to the supplier’s perspective and showing empathy for their situation, supplier quality engineers can create a more collaborative and productive environment for problem-solving. Working together, they can identify the root cause of quality issues using techniques like the 5 Whys or Fishbone diagrams.
Relationship-Based Six Sigma
Building trust with suppliers through open and honest communication is essential for effective collaboration. By establishing shared goals and empowering suppliers to take ownership of the improvement process, supplier quality engineers can foster a sense of responsibility and commitment.
Communication-Centered Statistical Process Control
Clear and concise communication is vital for ensuring that all parties involved understand the data and control charts used in SPC. By providing constructive feedback and working collaboratively with suppliers, supplier quality engineers can effectively address process variations.
Adaptive FMEA
Flexibility and adaptability are key in applying FMEA to different supplier situations. By involving suppliers in the FMEA process and continuously reviewing and updating risk assessments, supplier quality engineers can ensure that the technique remains relevant and effective.
Negotiation-Driven DOE
Negotiation skills are essential for conducting effective design of experiments. By seeking win-win outcomes, compromising when necessary, and considering long-term relationships, supplier quality engineers can ensure that DOE experiments are beneficial for both the supplier and the organization.
Cultural Sensitivity in TQM
Respecting cultural differences and adapting the TQM approach to align with cultural norms and practices is crucial for successful implementation. By ensuring inclusive participation and avoiding cultural imperialism, supplier quality engineers can create a more positive and effective working environment.
By integrating soft skills into these problem solving techniques, supplier quality engineers can build stronger relationships with suppliers, improve communication, and more effectively address quality issues. This ultimately leads to better quality products and services for the organization.
Subscribe to our newsletter.
Your go-to destination for insights, best practices, and innovative solutions in supplier quality assurance.
Recent Posts
How Kiuey simplifies PPAP and APQP compliance
August 21, 2025
AIAG vs VDA AIAG PFMEA? Know the differences between
July 23, 2025
Categories
Let's talk to see how PPAP Manager can help your company to save time and money.