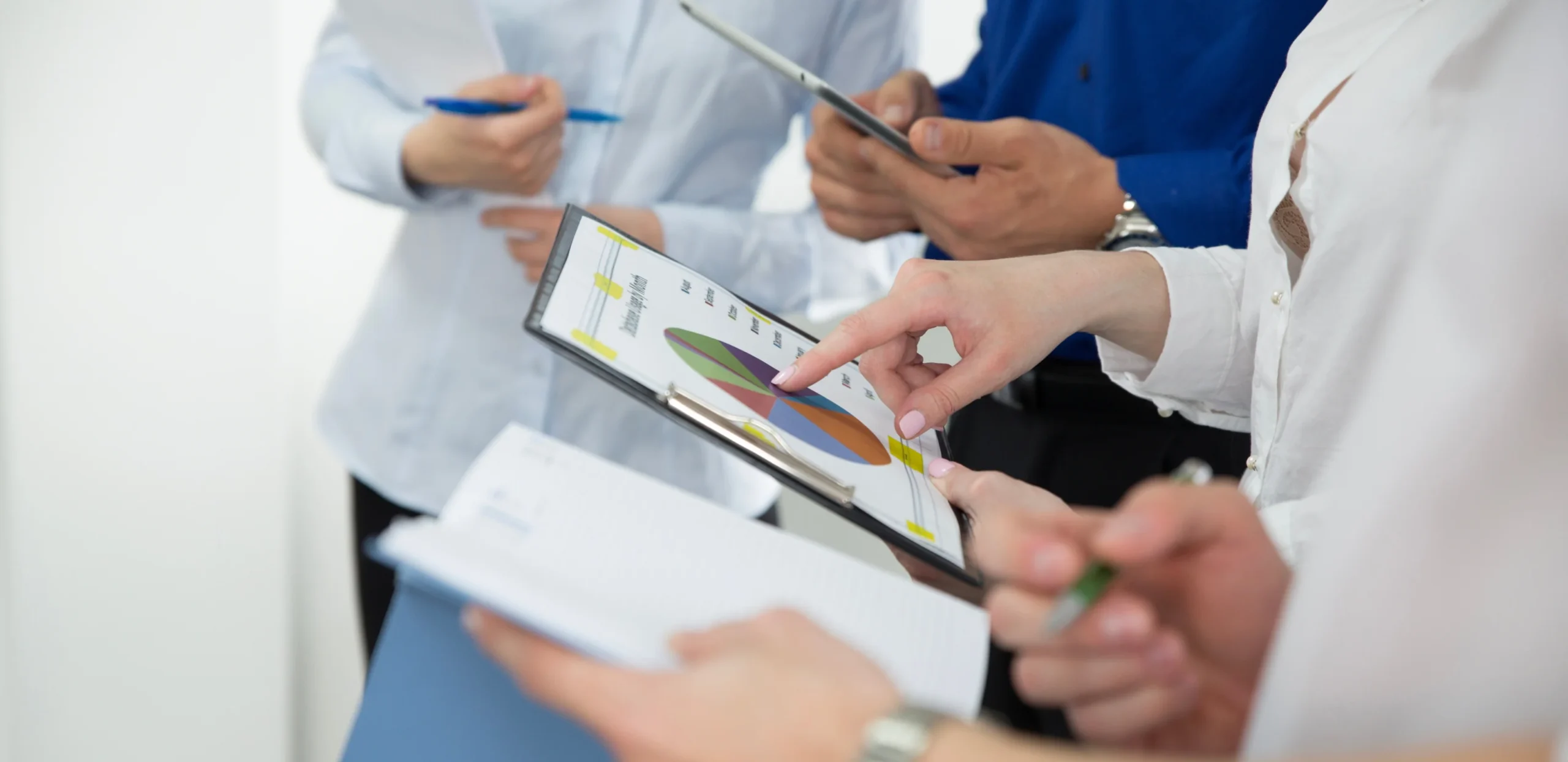
What is SCAR in quality management and how to handle it?
The Supplier Corrective Actions Request (SCAR) has a vital role in quality management, as it strongly impacts supply chain efficiency and customer satisfaction. More than just a document, it’s a process that allows manufacturers to maintain quality standards and uphold their suppliers to specific industry requirements whenever they fail to meet them.
The consistent occurrence of quality-related issues that SQEs face on the job further emphasizes the significance of understanding the intricacies of the SCAR process.
Non-compliance days are over. Learn how to properly manage supplier performance and maintain quality standards using the SCAR process, in this article.
What is a Supplier Corrective Action Request (SCAR)?
SCAR is a formal request issued to a supplier to address and rectify a quality issue or non-compliance. This process begins with identifying the problem, either during a supplier audit, through incoming material inspection, or as a result of a customer complaint. A comprehensive document describing the concern is then delivered to the supplier, who is expected to conduct a root cause analysis and propose corrective measures.
SQEs often engage with the SCAR process as part of their regular responsibilities, although the frequency can vary depending on the industry and the complexity of the supply chain.
This systemic approach improves quality management efficiency by establishing a structured framework for problem-solving between suppliers and manufacturers, while ensuring adherence to quality standards and preventing future error recurrence.
Key components of an effective SCAR document
A SCAR’s impact directly responds to the information it contains: an adequate combination of data paints a clear picture of what the non-compliance is and how to address it.
These are some of the main SCAR components, among varying templates:
- Supplier information: Includes name, contact, and other relevant identifiers.
- Clear non-compliance description: Provides a thorough explanation of the identified quality problem, its impact, location, detection date, and parties involved.
- Product details: Describes the affected material, process or service, unmet quality standards or requirements, and the scope of the issue.
- Root Cause Analysis: Contains preliminary findings and results derived from problem-solving techniques, such as the 5 Whys and Fishbone diagram.
- Corrective action plan: Outlines a request for immediate containment measures, long-term corrective actions, preventive steps, and timelines for implementation.
The role of SCAR in proactive quality improvement
Using SCAR data for trend analysis
SCAR data allows manufacturers to identify recurring quality problems, specific suppliers frequently involved in non-compliance, or common root causes across multiple cases. Monitoring how suppliers respond to SCARs over time can reveal trends in their corrective actions, responsiveness, and commitment to quality improvement. By analyzing historical SCAR data, organizations can forecast potential future risks and proactively mitigate them.
Integrating SCAR into the broader QMS
SCAR also plays an essential role in the broader quality management system, ensuring cohesive quality control and improvement throughout the supply chain. From audits, to supplier evaluations, and continuous improvement initiatives this process provides valuable insights into a supplier’s performance and reliability, through documentation and analysis.
In essence, the SCAR process acts as a bridge between core QMS elements, ensuring that issues are identified, addressed, and leveraged for sustained improvement.
Streamline your SCAR management process with Kiuey
Managing Supplier Corrective Action Requests effectively is crucial for ensuring consistent quality standards and building strong, reliable supplier relationships. However, it’s no secret the traditional SCAR processes can be time-consuming and riddled with inefficiencies.
Gain actionable insights at your fingertips with a comprehensive quality management software solution. Say goodbye to messy email chains, missed updates and manually juggling tasks: Kiuey automates key steps in the SCAR process—like assigning corrective actions, tracking deadlines, and sending reminders—so you can focus on what really matters.
Discover how Kiuey’s SCAR Manager software solution can help you optimize workflows and achieve greater quality outcomes today. Streamline quality management in your organization and start saving up to 50% resources with Kiuey.
Subscribe to our newsletter.
Your go-to destination for insights, best practices, and innovative solutions in supplier quality assurance.
Recent Posts
How Kiuey simplifies PPAP and APQP compliance
August 21, 2025
AIAG vs VDA AIAG PFMEA? Know the differences between
July 23, 2025
Categories
Let's talk to see how PPAP Manager can help your company to save time and money.