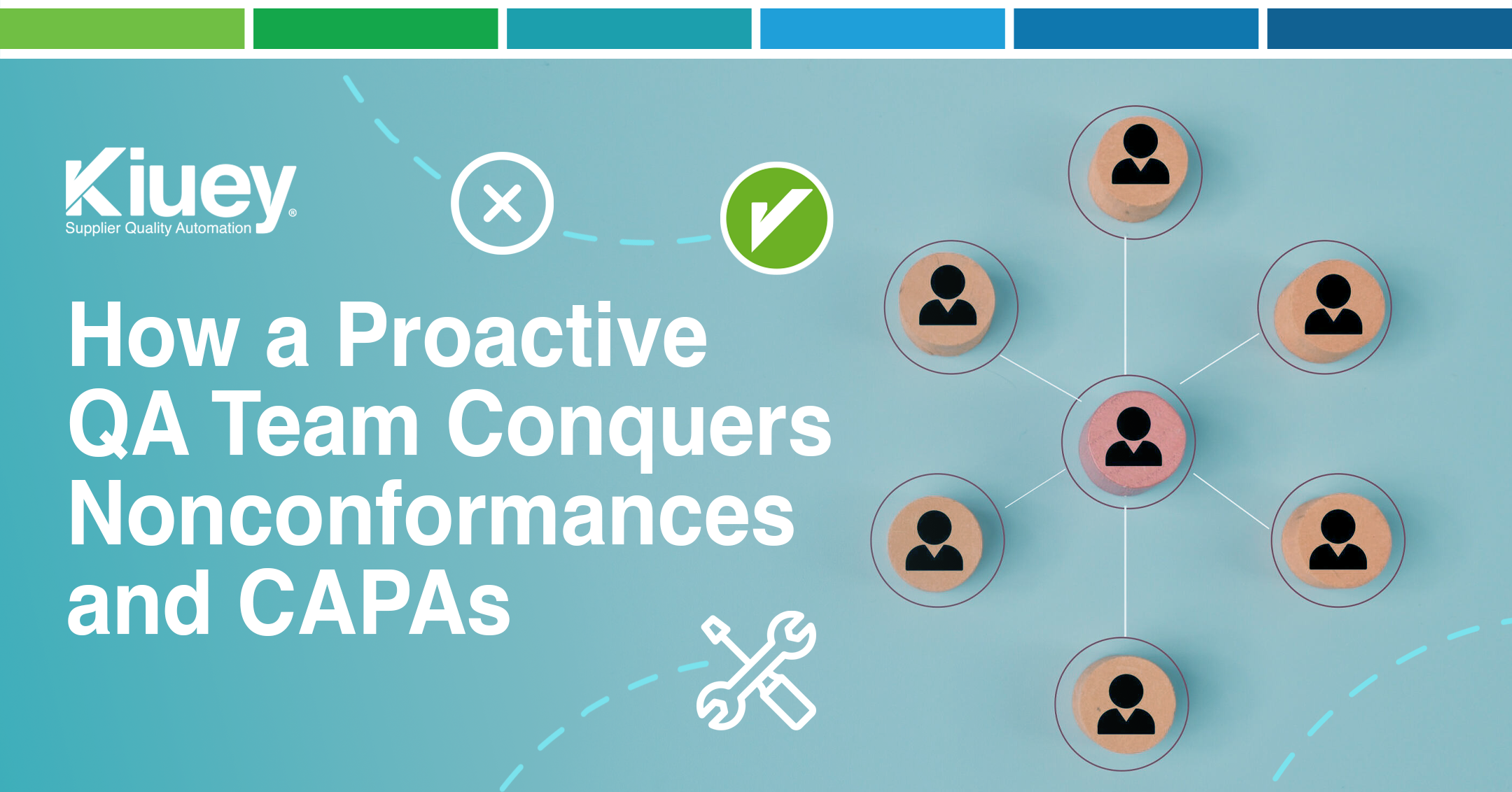
The Power of Engagement: How a Proactive QA Team Conquers Nonconformances and CAPAs
In the world of manufacturing, quality is everything. Even minor deviations from specifications, known as nonconformances, can have a ripple effect, impacting product safety, functionality,[…]
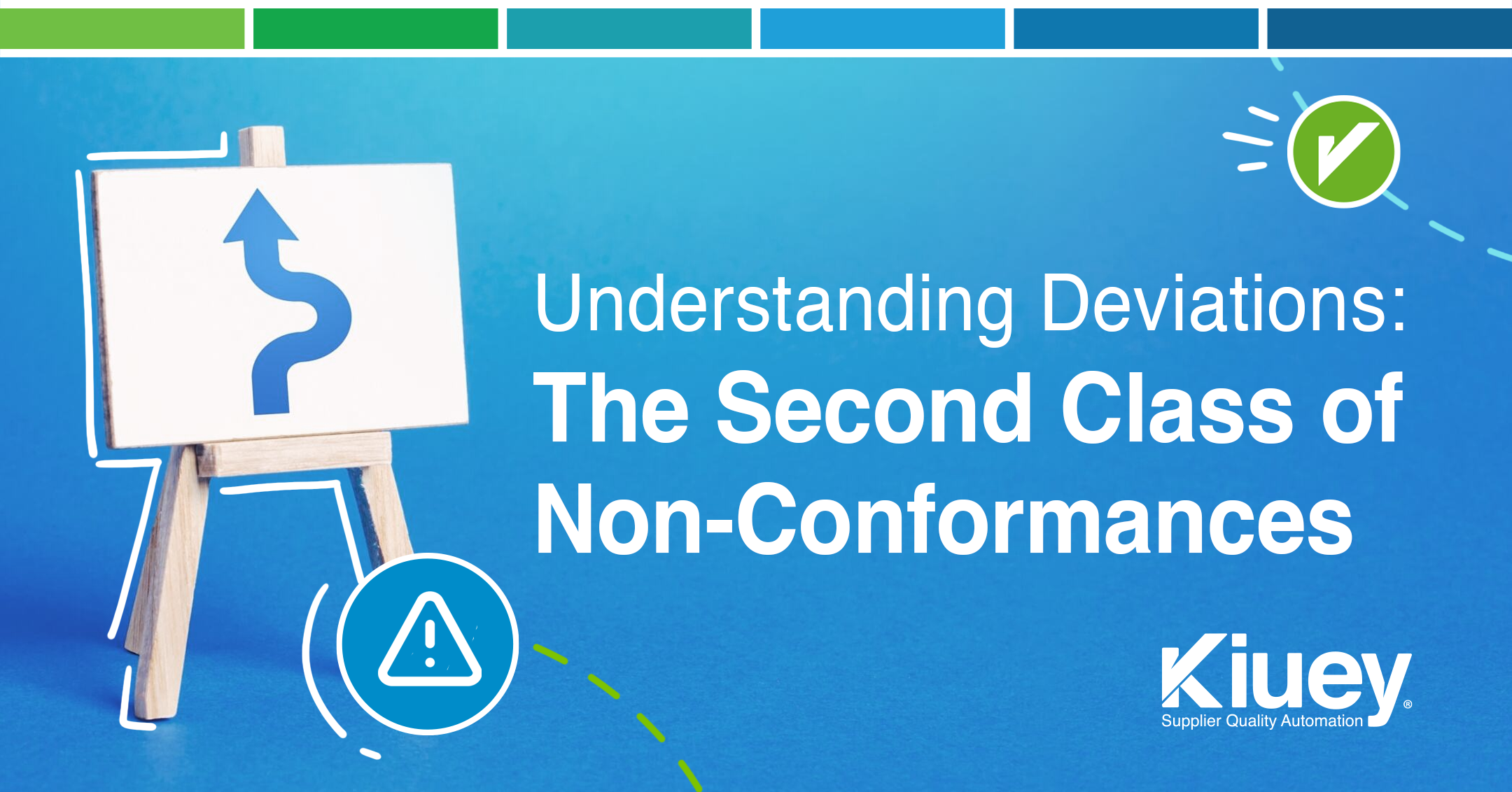
Understanding Deviations (Issues) in Manufacturing: The Second Class of Non-Conformances
In the relentless pursuit of quality, manufacturing thrives on consistency and adherence to specifications. However, even the most well-oiled production line can encounter hiccups. This[…]
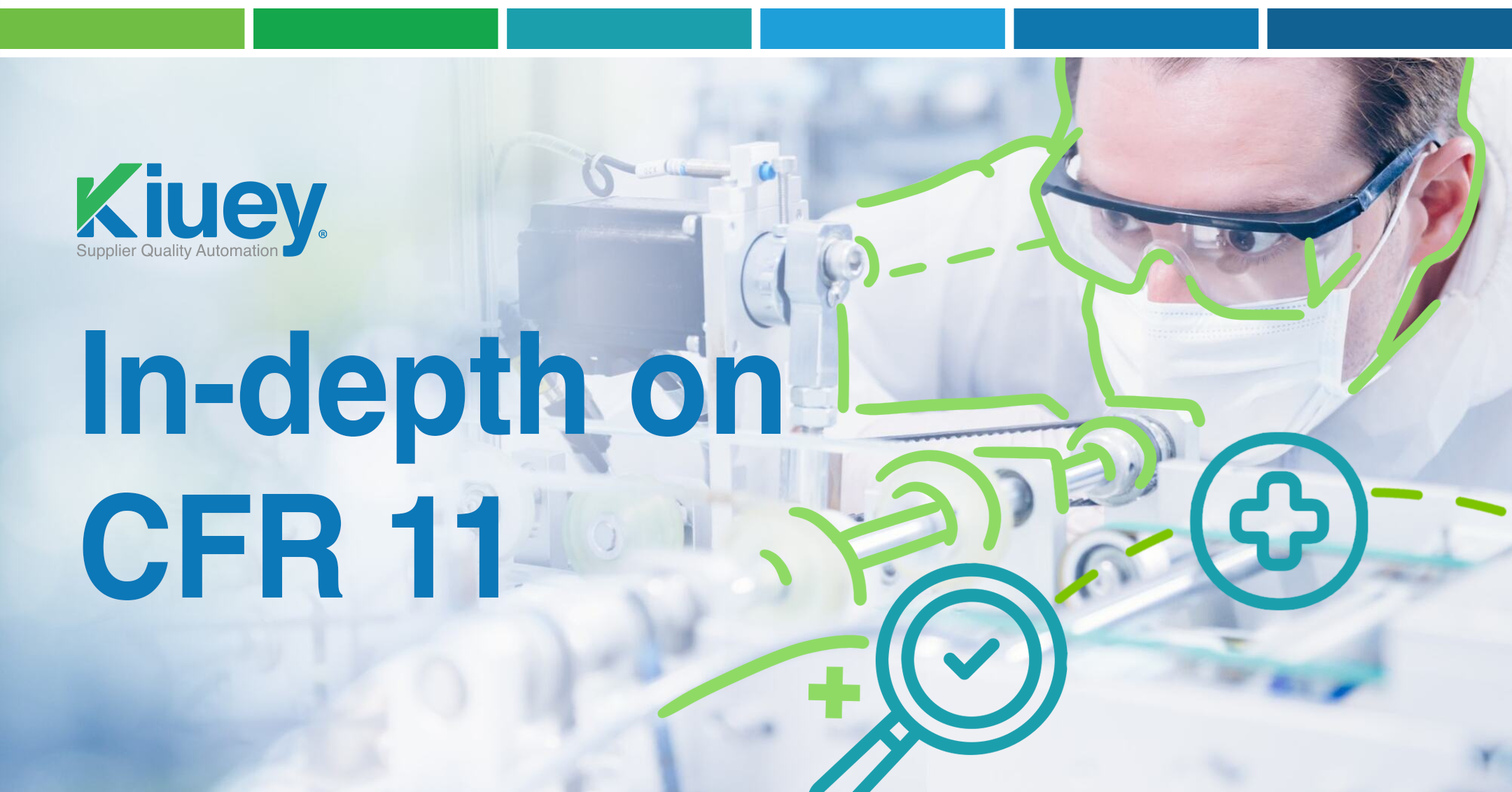
In-depth on CFR 11
The U.S. Food and Drug Administration (FDA) plays a vital role in protecting public health by regulating medical devices. Part 11 of Title 21 of[…]
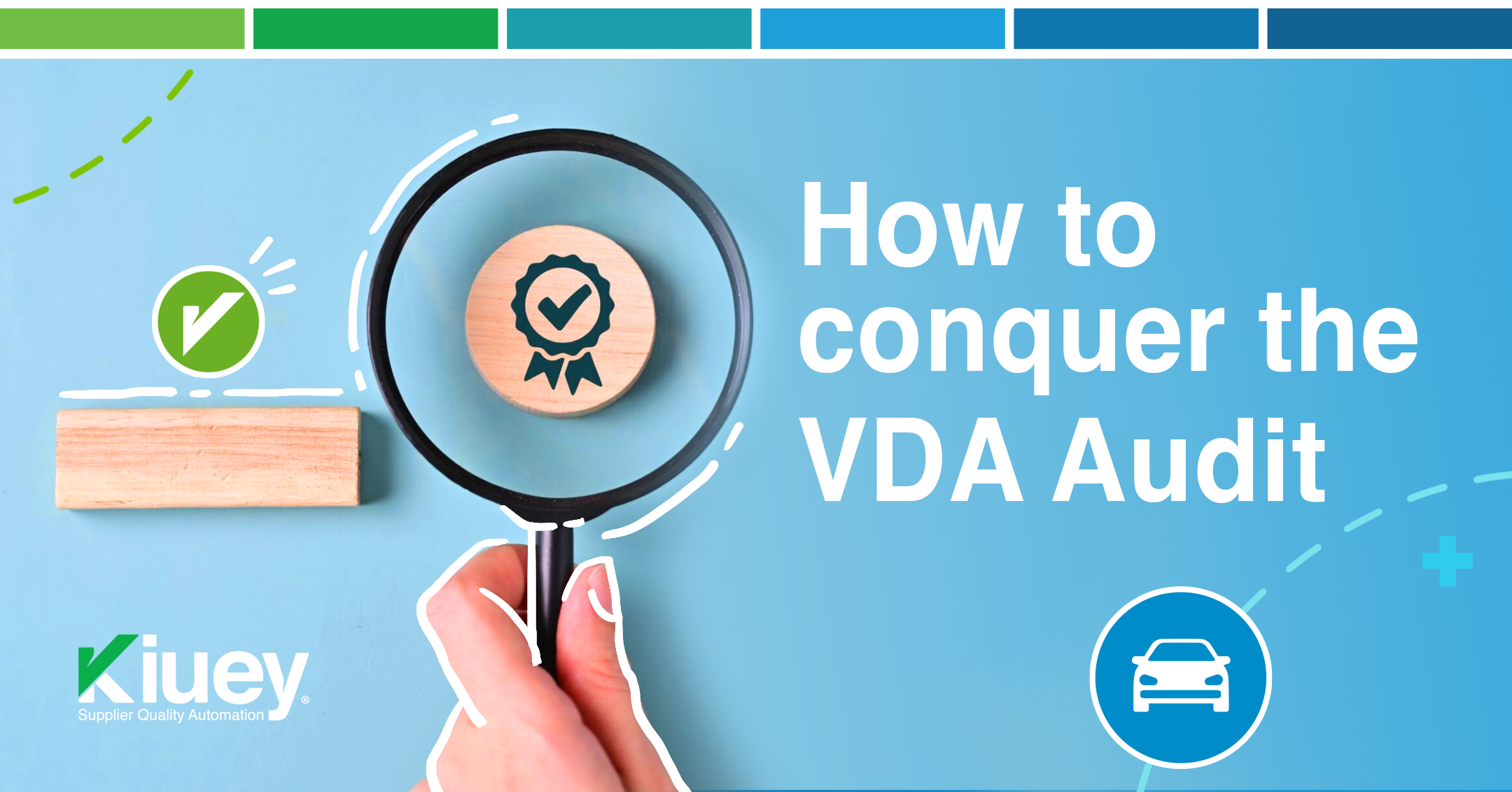
Conquering the VDA Audit: A Supplier Quality Engineer’s Guide
The automotive industry is a global machine, and for suppliers in the United States, understanding the quality standards set by international organizations like VDA (Verband[…]
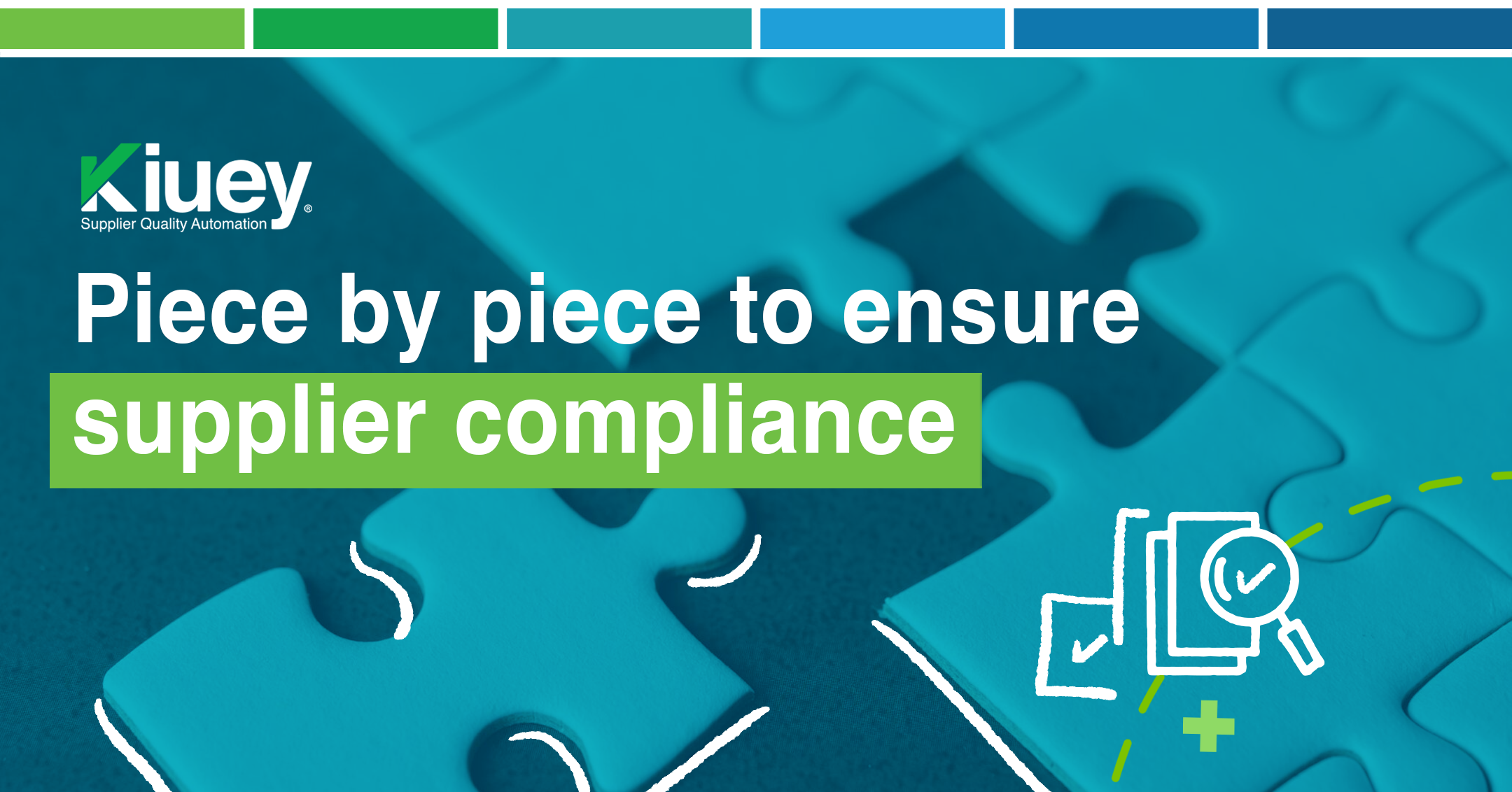
How to ensure supplier compliance, piece by piece
The manufacturing industry thrives on a well-oiled supply chain. Raw materials, parts, and components flow seamlessly from suppliers to production lines, ensuring finished goods reach[…]
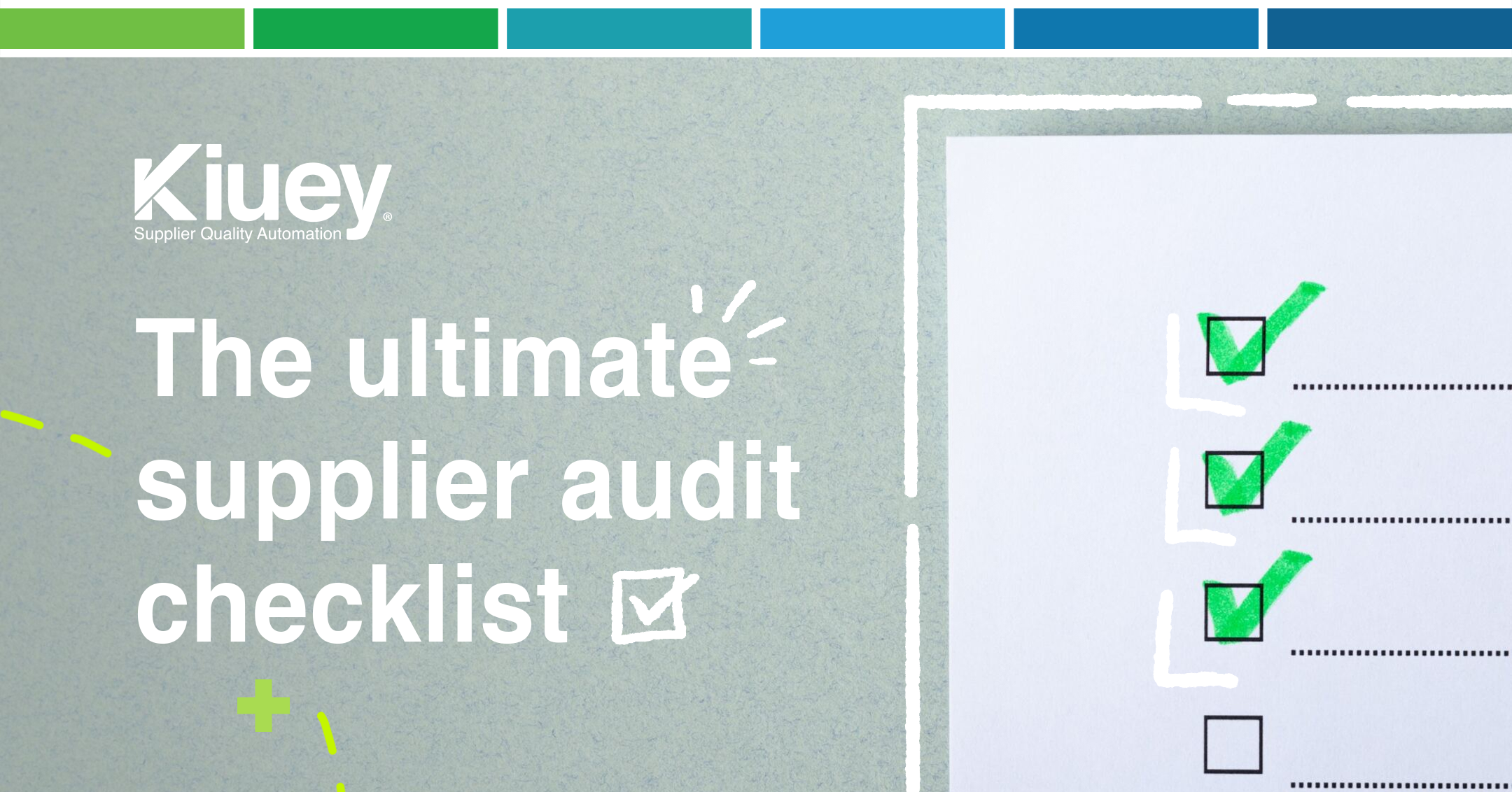
The ultimate supplier audit checklist
A robust supply chain is the backbone of any successful manufacturing operation. But a smooth flow of materials and parts hinges on one crucial factor:[…]
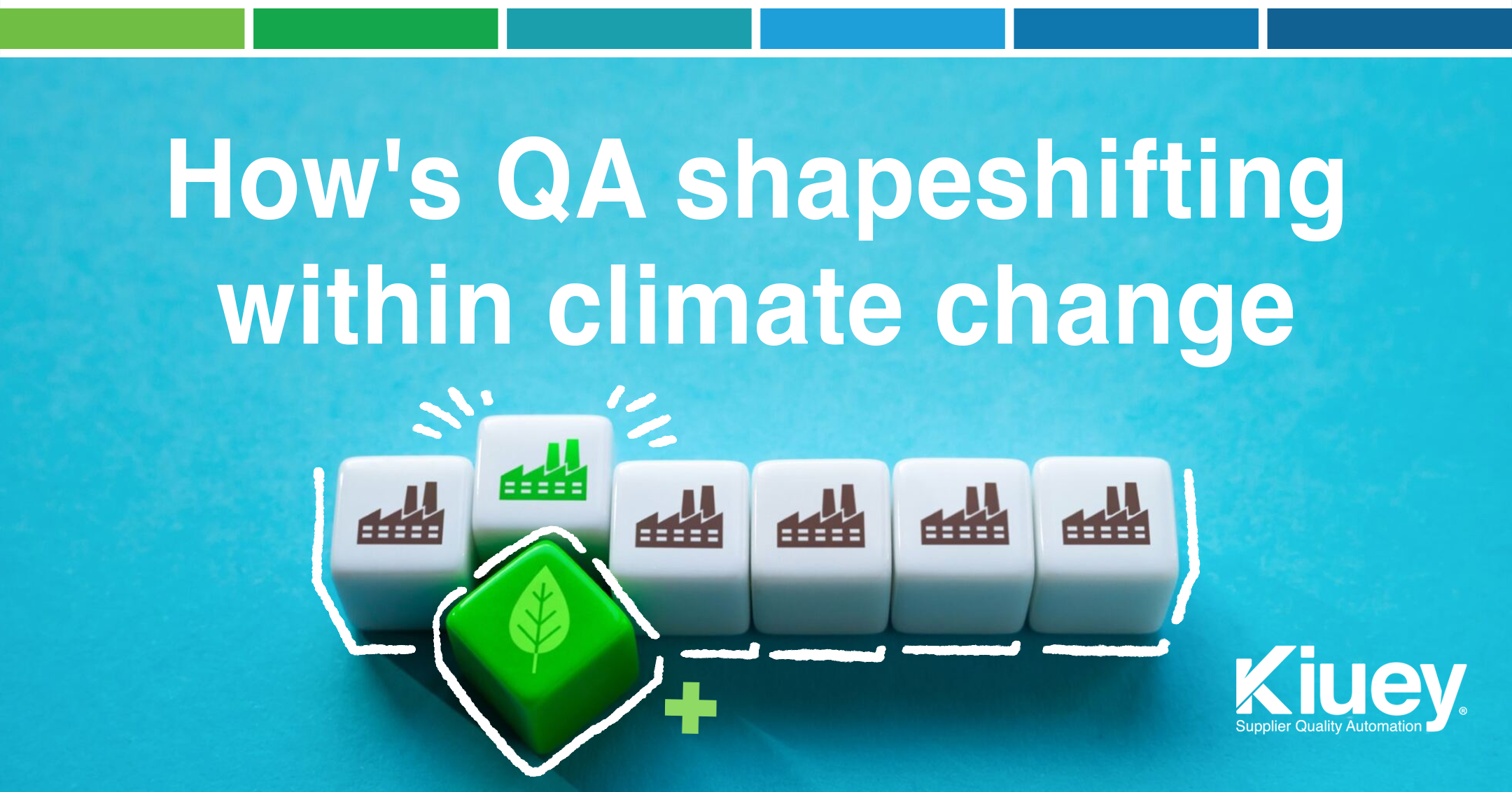
How’s QA shapeshifting within climate change in manufacturing
The industrial revolution ushered in an era of unprecedented progress, yet its legacy also includes a heavy footprint on the environment. Climate change, a consequence[…]
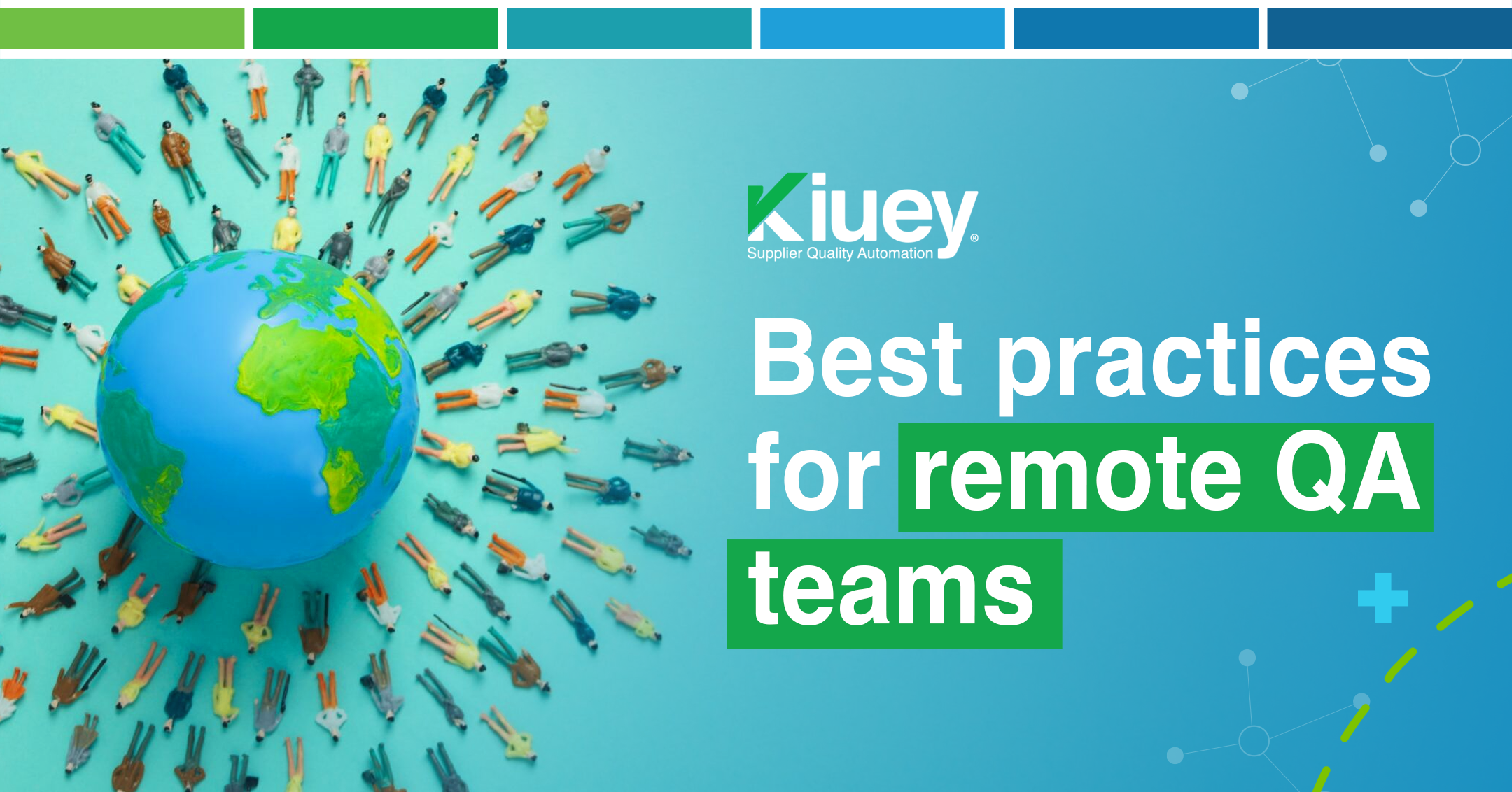
Boosting Productivity: Best Practices for dispersed and remote QA teams
The landscape of quality assurance (QA) is evolving. Remote work is no longer a novelty, and geographically dispersed QA teams are becoming increasingly common. While[…]
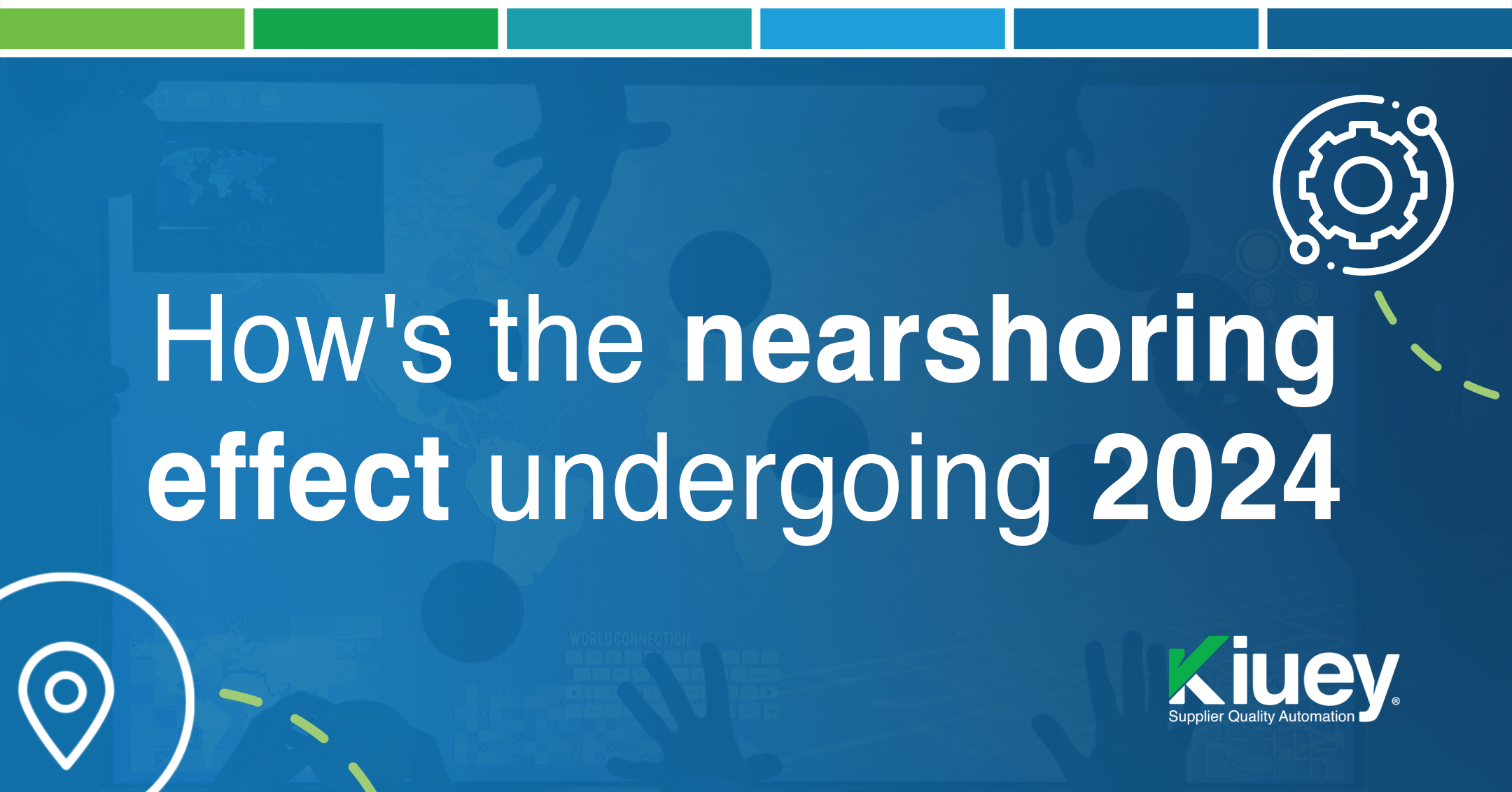
How’s the nearshoring effect undergoing 2024
2024 is witnessing a tectonic shift in the global manufacturing industry driven by the surging trend of nearshoring. This strategy involves companies strategically relocating production[…]
Subscribe to our newsletter.
Your go-to destination for insights, best practices, and innovative solutions in supplier quality assurance.
Recent Posts
The ROI of Lean ISO Management Systems
January 31, 2025
The Power of Second Chance Manufacturing Programs
January 30, 2025
The Secret to Customer Delight: Embedded Quality
January 28, 2025
The Psychological Impact of Stress on Quality Outcomes
January 28, 2025
Categories
Let's talk to see how PPAP Manager can help your company to save time and money.